Micro-barbs could make shots less painful
The 4-D-printed devices help drug-delivering needles stick to skin to give shallower shots
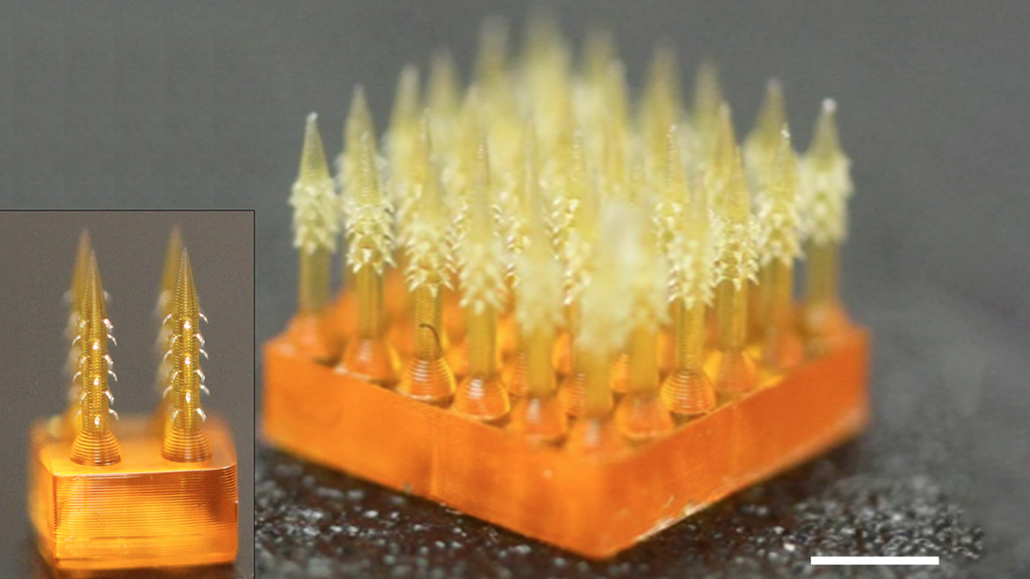
The tiny barbs on these needles anchor the device to skin. It allows the needles to deliver shots at a fraction of the depth of ordinary ones.
Riddish Morde
No one likes getting shots. “They’re painful,” says engineer Howon Lee at Rutgers University in Piscataway, N.J. “I hate them, and everyone hates them.” But they’re an effective way to deliver protective vaccines and medicines. So Lee has helped develop a new type of microneedle — one that can barely be felt.
Scientists have been working on miniature needles for years. The idea is to deliver a liquid drug, but with a needle so small it doesn’t sting. A microneedle pokes into the skin just a fraction as deeply as an ordinary needle. But this has had a downside, too. Most such devices are smooth, notes Lee. They can’t stay put long enough to deliver a full dose.
That’s where Lee’s work is different. His group unveiled a new microneedle device that can stick to skin longer. Its secret? The team added backward-facing barbs to the surface of the needles. These barbs anchor the device in the skin. Lee’s group described its innovation March 10 in Advanced Functional Materials.
Nature-inspired design
“Barbs” may sound painful, but don’t worry. They stick out only about 450 micrometers (0.02 inch). That’s about the thickness of a pinkie nail.
Biting creatures in the wild inspired the design. “How can we mimic the way nature does things?” Lee asks. A mosquito siphons blood with a needle that has jagged spurs on its surface. Worms use a swollen feeding tube, called a proboscis (Proh-BAA-sis), to anchor themselves in walls of the gut. Honeybee stingers have backward barbs.
“We know nature is really good at doing this stuff,” says Candice Majewski. “So mimicking nature is a good approach to design.” Majewski is a mechanical engineer at the University of Sheffield, in England. She did not work on the new design.
The researchers tested their barbed device by sticking it into raw chicken, then pulling it out. The “stickiest” design had six microneedles per row, each needle with its own cluster of barbs. With this setup, they reported, their device proved stronger than other microneedle designs.
Printing in 4-D
Lee began working on the project in 2016 with engineer Giuseppe Barillaro at the University of Pisa, in Italy. Barillaro had been working on microneedles for years. And Lee had experience with 3-D printing.
The engineers used a kind of 3-D printing to create the microneedles. 3-D printing involves making an object by building it up, layer by layer. For the “ink” in this printer, the researchers used a special solution that combines a material called a polymer with a light-absorbing chemical. This mixture hardens and becomes strong when exposed to ultraviolet light. For their process, they printed a layer of solution, strengthened it with that UV light, then added the next layer. They repeated these steps over and over to build the whole object.
To make the microneedle’s barbs, the researchers took advantage of a curious effect of this type of 3-D printing. If applied in a thick layer, the solution doesn’t solidify evenly. The surface becomes uneven or curved. Knowing this, the scientists printed thick barbs sticking out horizontally from the main shaft of the microneedle. On exposure to ultraviolet light, the barbs curved downward.
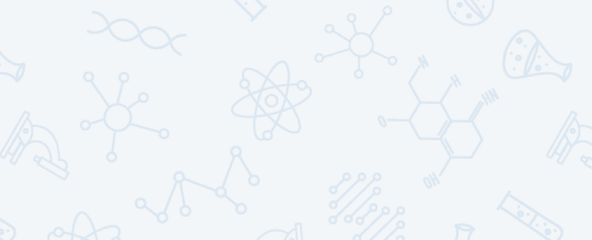
Educators and Parents, Sign Up for The Cheat Sheet
Weekly updates to help you use Science News Explores in the learning environment
Thank you for signing up!
There was a problem signing you up.
The group didn’t find success right away, Lee notes. Finding the right material to use was tricky. 3-D printers print with heated liquid that cools to become solid. Here, they had to find a material that would become solid and strong, but still bend without breaking when exposed to light.
Majewski develops new applications for 3-D printing. The new work shows how scientists are getting smarter about ways to use it, she says. Since the device changes shape after it’s printed, the engineers describe their method as “4-D printing.” (The fourth dimension is time, since the device changes shape after printing.)
Majewski says, “4-D printing is becoming more common.” Through years of trial and error, engineers are learning how different materials behave when they’re printed. And that enables them to print objects that can change — like the barbs — even after they’re created. “These advances come from a better understanding of what’s going on, scientifically, in the printing process.”
This is one in a series presenting news on technology and innovation, made possible with generous support from the Lemelson Foundation.