A soil-based ‘concrete’ could make buildings green, even on Mars
The goal is to come up with an ‘ink’ for 3-D printing that’s dirt cheap
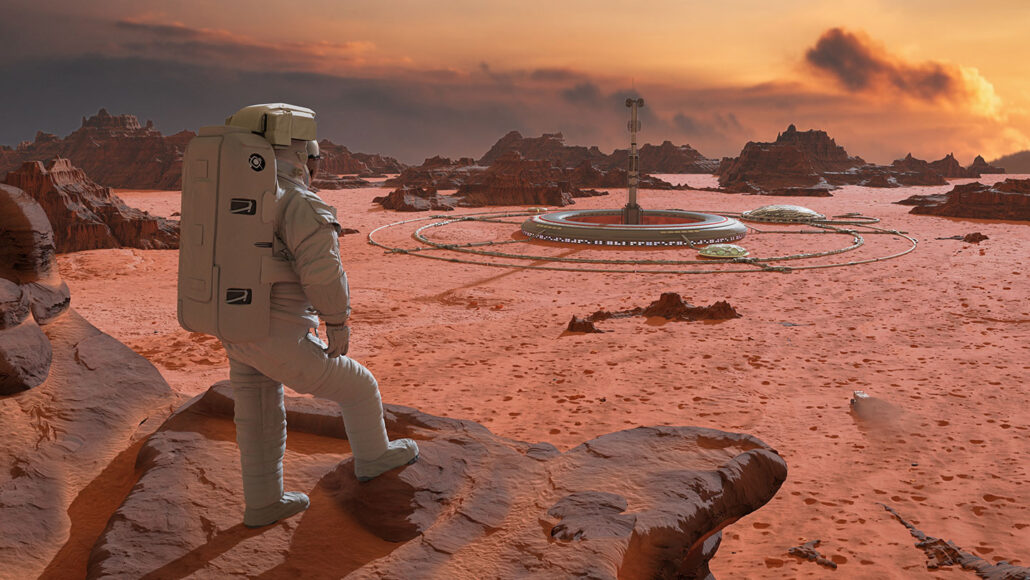
Human settlements on Mars are still just science fiction. But in the future, people might 3-D print buildings there, as on Earth, using a newly discovered alternative to concrete.
dottedhippo/iStock/Getty Images Plus
Tech advances have been moving 3-D printers from labs and maker shops into factories. Now researchers have developed a soil-based “ink” for 3-D printing. The novel material can take the place of concrete in constructing new buildings.
“Concrete is one of the most widely used construction materials by far,” notes Aayushi Bajpayee. But from an environmental standpoint, it’s not very green. Roughly 5 to 8 percent of greenhouse-gas emissions from human activities trace back to concrete. The cement that holds concrete together releases lots of carbon dioxide, a greenhouse gas. The process also takes huge amounts of energy, which tend to come from fossil fuels. Builders also typically transport concrete over long distances. That travel burns still more fossil fuels.
Bajpayee is a chemist and graduate student at Texas A&M University in College Station. She and chemist Sarbajit Banerjee, also at Texas A&M, described their new greener alternative to concrete on August 20 at the American Chemical Society’s fall national meeting.
Previously, Banerjee and others had shown how to make a material for roads with a bog-like muskeg soil. They found it in northern Alberta, Canada. They added cellulose fibers from local plants to the soil. By substituting some of that soil for other materials, they cut costs, in part by hauling in fewer heavy supplies from far away.
“Cellulose is part of the glue that holds together soil particles. [It] allows us to devise a printable ‘ink,’” Banerjee says. After drying, he notes, that ink will later be able to support heavy loads, as walls and other construction materials must. Sodium silicate and a strong alkaline (high pH) compound also went into the mix. Those last two ingredients formed a network of chemical links throughout the mix. Those cross-links held the material together, making it strong.
The researchers’ new material uses a common Texas clay soil and local plants. Both are different than those used earlier in Canada. But the goal was similar: Use mostly local materials to create strong concrete alternatives. And make the fast-setting material flow well for 3-D printing.
The team dried the clay soil and ground it up. A sieve then got most of the soil bits down to a tiny size. The team mixed the clay bits with sodium silicate, cellulose and an alkaline liquid. The mix also included a byproduct from processing sugar beets. Its job is to the material swell up later when they added water.
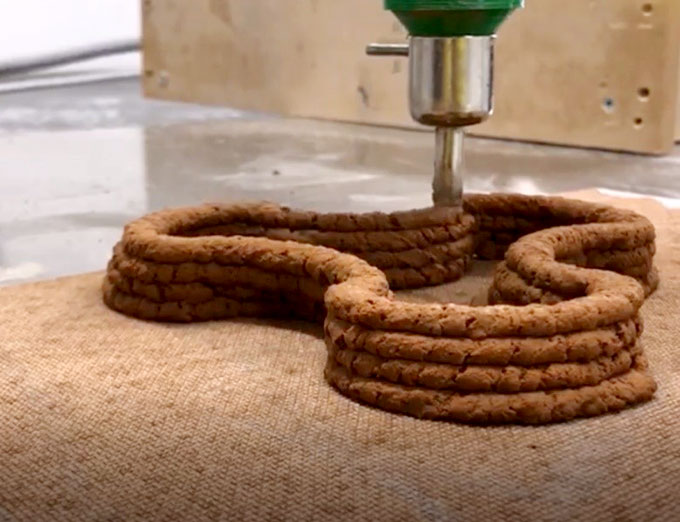
From the ground up
A 3-D printer creates an item, one layer upon another. To print a building, construction would literally build from the ground up. As the soil-based “ink” exits the printer, “it feels like whipped cream,” Bajpayee says. But she adds that “it holds its shape.” And it hardens quickly, so it won’t flatten as the next layer is printed atop it.
Earlier, the team published details of its success establishing the process. They appear in the March 10, 2020 Frontiers in Materials.
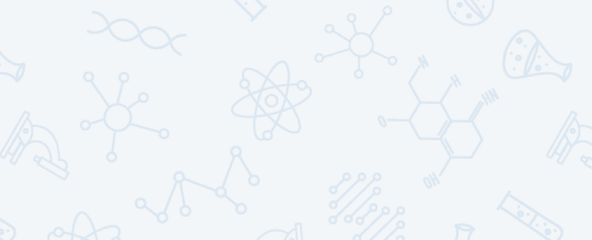
Educators and Parents, Sign Up for The Cheat Sheet
Weekly updates to help you use Science News Explores in the learning environment
Thank you for signing up!
There was a problem signing you up.
Banerjee thinks the process could work with soils at many sites. His group has even tried a few tests with simulated Martian soil. After all, local materials would be most practical if people ever build outposts on the Red Planet. That work could be tricky, however, because radiation makes the planet’s soil very clumpy, he says. Another challenge: Mars doesn’t have readily available organic materials, such as cellulose. That could make it harder to get the soil particles to stick together and flow properly. The team is looking for a fix.
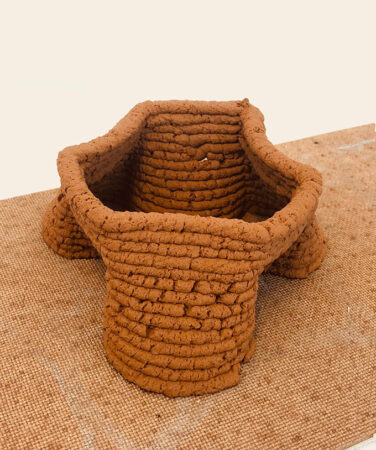
Meanwhile, Banerjee is excited about the prospects for printing structures on Earth with the new soil-based inks.
Any shape should be possible, “so this is really an architect’s dream,” he says. The model he and Bajpayee showed off at the ACS meeting has a series of dramatic curves — ones that would have been hard to build with concrete. The process would have to be scaled up much more to 3-D print an actual building.
The team is also thinking ahead. Eventually a road or building may no longer be needed. Then this printed material can be broken down into mostly non-toxic materials, Banerjee says.
For now, the team is looking at using 3-D printing to construct the outer walls of buildings. Other parts must meet building codes (rules that outline how buildings should be made). Most existing codes were written for concrete, Bajpayee notes. New codes will be needed to outline how this material would have to perform.
“The overall concept is novel, and I applaud the team on their innovative idea,” says Xiong (Bill) Yu. He’s a civil engineer at Case Western Reserve University in Cleveland, Ohio. More research will be needed to better understand where and how the material can be used, he says. For instance, how much weight can it hold and how might it hold up to climate extremes?
Cost, of course, is another big unknown. Bajpayee agrees. As she notes, “My whole research is about sustainability and striving to make it dirt cheap.”