Rare-earth mining is dirty but key to a climate-friendlier future
That’s spurring new research to offer a steady but safer supply of these precious metals
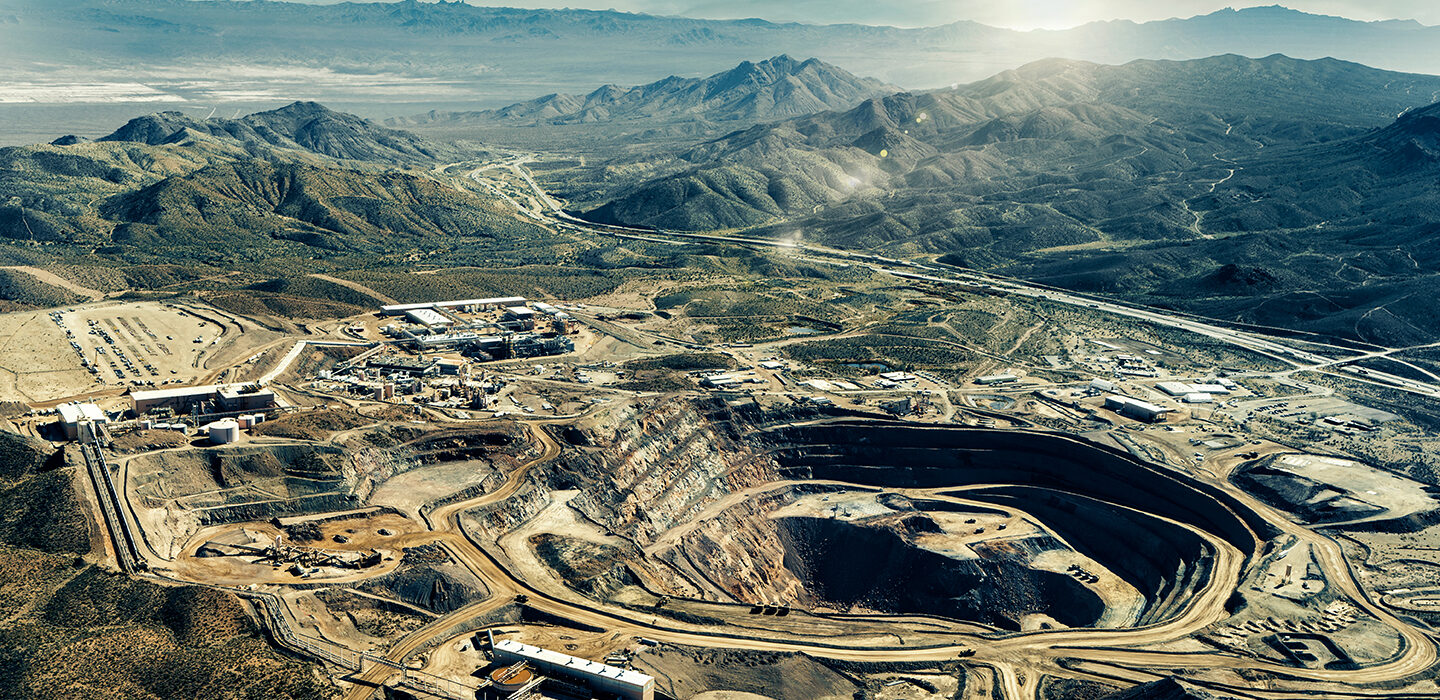
Mountain Pass (shown), in southeastern California, remains the United States’ only mine for rare earth elements, the building blocks of magnets used in smartphones, wind turbines and electric vehicles.
TMY350/WIKIMEDIA COMMONS (CC BY-SA 4.0)
In spring 1949, three prospectors armed with Geiger counters set out to hunt for treasure. They were roaming the arid hills of southern Nevada and southeastern California.
In the 1800s, these mountains yielded gold, silver, copper and cobalt. But these men were looking for something more valuable — uranium. It was the beginning of the Cold War, and the United States was looking to build up its arsenal of nuclear weapons. Mining homegrown uranium was thus seen as a matter of national security.
After weeks of searching, the trio’s instruments detected intense radioactivity. But it wasn’t uranium.
The brownish-red veins were rich in something else. They contained fluorine, carbon and 17 curious metals known as rare earths. Also in the ore were traces of radioactive thorium. That’s what had set their Geiger counters pinging.
The prospectors ultimately sold their claim to the Molybdenum Corporation of America. Later called Molycorp, it was interested in rare earths. By the mid-20th century, these metals were proving quite useful. Cerium, for example, was the basis for a glass-polishing powder. Europium lent glowing phosphors to the screens of recently invented color TVs and fluorescent lights.
For the next few decades, this site — Mountain Pass mine — would become the world’s top source for rare-earth elements. That started changing in the late 1980s. China was now mining its own rare earths and in huge quantities. It also was selling them at a lower cost. Then a series of toxic-waste spills brought mining at Mountain Pass to a halt in 2002.
But the green-tech revolution has renewed interest in Mountain Pass. It reopened and remains the only U.S. mine for rare earths.
These metals are now at the heart of many clean energy technologies, including wind power and electric vehicles. Such tech doesn’t emit a lot of climate-warming greenhouse gases. Rare earths are also a prime player in most of today’s smallest, fastest and most advanced electronics.
In fact, U.S. mining of rare earths has emerged as a new issue of national security. That’s according to a Feb. 24, 2021, report by President Joe Biden’s administration.
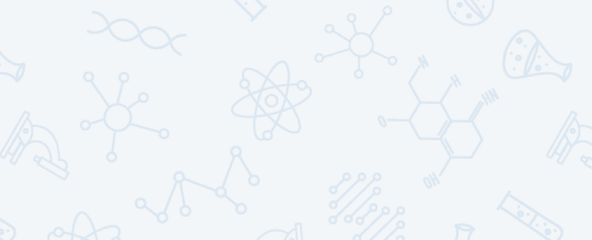
Educators and Parents, Sign Up for The Cheat Sheet
Weekly updates to help you use Science News Explores in the learning environment
Thank you for signing up!
There was a problem signing you up.
Not so rare after all
Despite their name, rare earths are not actually rare. They just tend to show up in very low concentrations.
On their own, these ores have little value. To find use, that ore must undergo complex processing, notes Julie Klinger. She’s a geographer at the University of Delaware in Newark. This processing uses a lot of energy, which emits a lot of greenhouse gases. It also uses lots of water and relies on toxic chemicals. As a result, rare-earth mining has an environmentally dirty history.
Miners dig vast open pits. These pollute the environment and disrupt ecosystems. These operations can produce wastewater ponds filled with toxic acids, heavy metals and radioactive material. The waste ponds also will sometimes leak into water that might otherwise be used for drinking.
“We need rare-earth elements … to help us with the transition to a climate-safe future,” says Michele Bustamante. She’s a sustainability researcher at the Natural Resources Defense Council. It’s in Washington, D.C. Yet, she adds, every stage of rare-earth mining poses risks to the environment.
A number of research teams now hope to change that.
Where are rare earths mined?
Few countries currently mine rare-earth elements (see map). But rare-earth ores have been identified in many other locations, including Vietnam, Turkey and Greenland.
Rare earth mining locations
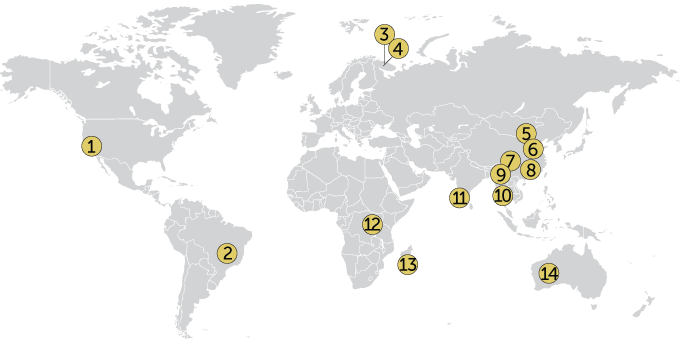
- Mountain Pass, Calif. (U.S.)
- Araxá (Brazil)
- Lovozero (Russia)
- Khibiny (Russia)
- Bayan Obo (China)
- Weishan (China)
- Maoniuping (China)
- Longnan (China)
- Northern Myanmar
- Thai Peninsula (Thailand)
- Chavara (India)
- Karonge (Burundi)
- Mandena (Madagascar)
- Mount Weld (Australia)
Mining’s big environmental footprint
Between the jagged peaks of California’s Clark range and the Nevada border sits a broad, flat valley known as Ivanpah Dry Lake. From about 1984 to 1998, this site served as a holding pen for wastes from mining at Mountain Pass.
A buried pipeline sent water containing toxic wastes — including radioactive thorium — some 23 kilometers (14 miles). This created evaporation ponds in and around Ivanpah’s dry lake bed. Over the years, that pipeline ruptured. Some 60 spills dumped an estimated 2,000 metric tons (2,200 U.S. tons) of wastes. Federal officials feared the wastes’ thorium might pose a cancer risk to people who lived or visited nearby.
In 1997, the mine’s owner was ordered to clean up the spills and pay fines. Shortly after that, mining at Mountain Pass stopped.
Meanwhile, half a world away, another environmental disaster was unfolding.
Since the 1990s, between 80 and 90 percent of rare-earth metals have come from China. Just one site there, the Bayan Obo mine, accounted for 45 percent of rare-earth production in 2019.
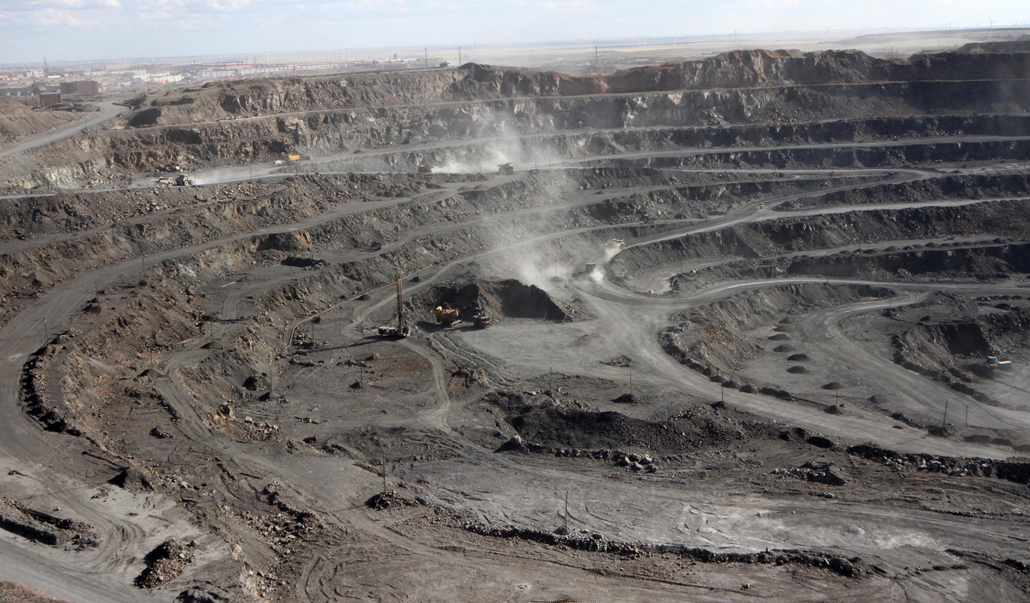
That mine spans 48 square kilometers (18.5 square miles). It’s also one of the most heavily polluted spots on Earth. By 2010, officials in the nearby city of Baotou noted that tailings — toxic mine wastes — were being dumped on farmland and into local waters. Tailings also entered the nearby Yellow River. Fumes and toxic dust polluted the air. People nearby complained of nausea, dizziness, migraines and arthritis. Some had skin lesions and discolored teeth. Others showed different signs of poisoning, such as brittle bones, notes Klinger at Delaware.
The country’s rare-earth industry was causing “severe damage,” China’s State Council wrote in 2010. It said the mines were causing a “destruction of vegetation and pollution of surface water, groundwater and farmland.”
Faced with these and other problems, in 2010 China cut its export of rare earths by 40 percent. This sent prices of the metals soaring across the globe. It also kicked off concerns that China could not be relied upon to supply nearly all of these must-have metals.
Suddenly, new interest in rare-earth mining emerged outside China. One site was a fossilized ancient volcano. Known as Mount Weld, it’s in Western Australia. Rare-earth mining there didn’t have anywhere near the environmental impacts as in China. This site was too remote and fairly small.
Sources of rare-earth elements over time
In the mid-20th century, the U.S. Mountain Pass mine was the world’s top source for rare-earth oxides. China began to dominate global production in the 1990s. In the last decade, the return of Mountain Pass along with the opening of Australia’s Mount Weld and production in Myanmar, Brazil and other locations have begun to shift that balance.
Global rare-earth production
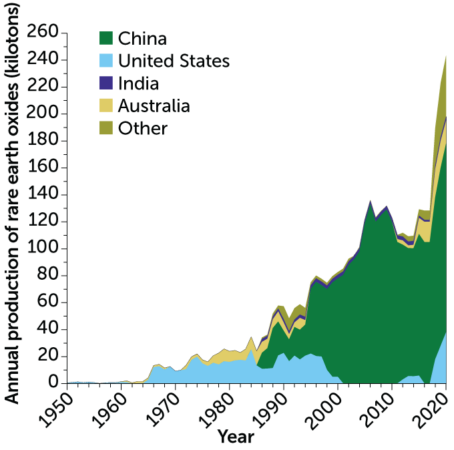
Mountain Pass mine gets new life
The United States, too, was eager to again mine rare earths. And Mountain Pass was still its best prospect.
The mine’s current owner resumed mining and used a new “dry tailings” process. But it was not profitable. In 2015, the mine went bankrupt. MP Materials bought it two years after that and the mining restarted. By last year, Mountain Pass was producing 15 percent of the world’s rare earths.
One hot morning last August, Matt Sloustcher stood at the edge of the mine. He’s a senior vice president of MP Materials. In front of him was a giant hole. At 800 meters (a half mile) across and almost a quarter that deep, it’s big enough to see from space.
From his vantage there, Sloustcher pointed out buildings. In one, ore gets crushed and ground up. In another, ground rocks are chemically treated to pull out as much non–rare earth material as possible. He also pointed to where water is squeezed from wastes and sent to lined ponds. What results is a concentrated ore rich in the rare-earth oxides used to make powerful magnets.
This ore is nowhere near the magnet-making stage. But the company has a plan to move from “mine to magnet,” says Michael Rosenthal. He’s the company’s chief operating officer. And he wants to again make the United States a leading source of rare earths.
Since coming online in 2017, Mountain Pass has shipped its concentrated ores to China for the next steps. These include the hard and hazardous process of separating one rare earth from another. But last November, MP Materials announced it had begun the first stages of bringing ore processing back to the United States.
One plant will pull lighter rare-earth elements out of the ore. These metals, such as neodymium, are key ingredients in the permanent magnets that power electric vehicles and many consumer electronics. A second plant will pull out the heavier rare earths. These, too, are used in magnets. This plant would extract yttrium, too, a rare earth used in superconductors and lasers.
Chemically, rare-earth elements are extremely similar. That means they like to stick together. Separating them is hard and leads to lots of toxic waste.
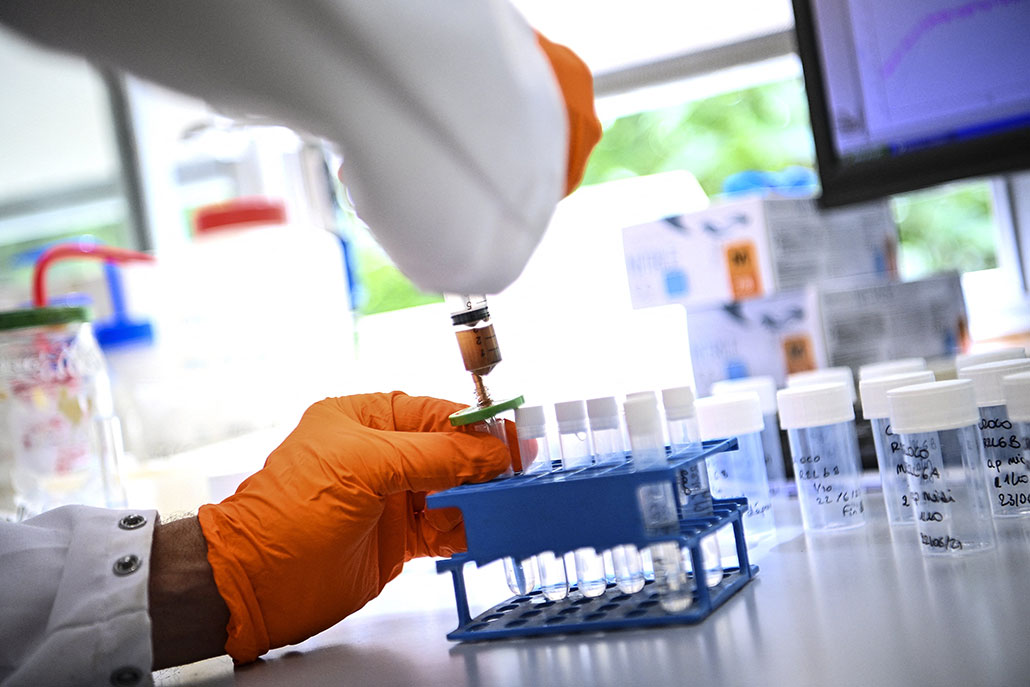
But one of the biggest issues is how inefficient the separation process is, notes Santa Jansone-Popova. She’s an organic chemist at Oak Ridge National Laboratory in Tennessee. Companies have to go through lots of steps to get a relatively pure rare-earth element.
Jansone-Popova is part of a team that has been hunting ways to cut down those many steps. Last year, her team identified a new chemical hook to snag certain rare earths. It works better than those now used in the industry.
“The path to the future has to do with getting the most out of what we take out of the ground,” says Bustamante at NRDC. That means using mined resources efficiently. It also means recycling rare earths from products no longer in use.
Recycling is a worthwhile goal, notes Saleem Ali. He’s an environmental planner who works at the University of Delaware in Newark. But, he adds, recycling is no silver bullet. For one, there aren’t enough spent batteries and other materials from which to recycle rare-earth metals. That’s why “some mining will be necessary,” he says. And the need for rare earths will only grow as the demand increases for the smartphones, magnets, electric vehicles and other products that rely on these precious metals.