Analyze This: Hardened wood can make sharp steak knives
Modifying wood may make a renewable material that can stand in for steel and plastic
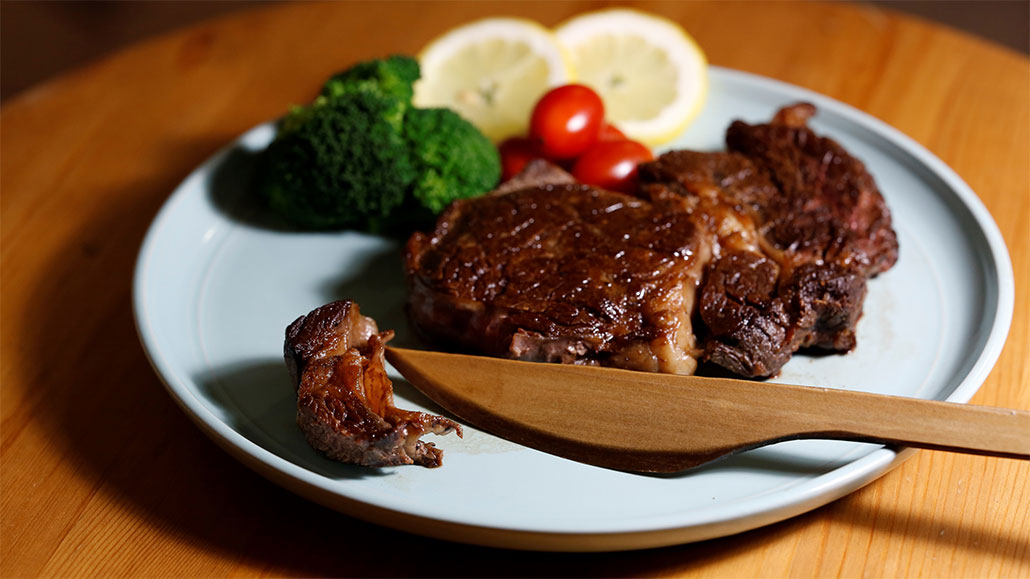
Removing some of wood’s lignin, one of its natural polymers, and squashing it makes a hard material. That wood now can be carved into a knife that will slice through steak, as here.
B. Chen
An age-old material has gotten a hardcore makeover. Researchers have modified wood to make a renewable substitute for plastic and steel. Carved to make a knife blade, the hardened wood is sharp enough to easily slice through steak.
People have built with wood for thousands of years, making houses, furniture and more. “But we found that the typical use of wood barely touches its full potential,” says Teng Li. A mechanical engineer at the University of Maryland in College Park, Li applies physics and materials science to design. He and his colleagues developed the hardened wood.
Materials such as diamonds, metal-containing mixes known as alloys and even some plastics are very hard. They aren’t, however, renewable. So Li and other scientists have been trying to make hard materials from living things, such as plants, which are both renewable and degrade easily.
Wood contains the natural polymers cellulose, hemicellulose and lignin. These polymers give wood its structure. Chains of lightweight and strong cellulose, in particular, make a skeleton of sorts for the wood. Li’s team came up with a way to enrich the wood in that cellulose. They first soaked blocks of basswood in a boiling solution. The solution contained chemicals that cut some of the chemical bonds between cellulose and the other polymers. But with lots of pits and pores, the block at this stage was soft and squishy, notes Bo Chen. A chemical engineer, Chen is part of the University of Maryland team.
His group then squashed the wood with a machine that applied a lot of pressure to smash the pores and remove the remaining water. After the wood was dried out with heat, Li says it became so hard that a fingernail couldn’t scratch it. The researchers then soaked the wood in oil to make it water-resistant. Finally, the team carved this wood into knives, either with the wood grain parallel or perpendicular to a knife’s edge. The scientists described this method October 20 in Matter.
The researchers compared their knives with commercial steel and plastic knives. They also made a nail from the treated wood and used it to hold together three wooden boards. The nail was strong. But unlike steel nails, Chen notes that the wooden nails won’t rust.
Testing for hardness
In the Brinell hardness test, a ball of a superhard material called carbide is pressed against the wood, denting it. The resulting Brinell hardness number is calculated from the size of the dent in the wood. Figure A shows the test results for natural wood (green) and hardened wood (blue) that had been treated with chemicals for 2, 4 and 6 hours. From the hardest of those woods, the researchers made two wood knives that they compared with commercial plastic and steel table knives (Figure B).
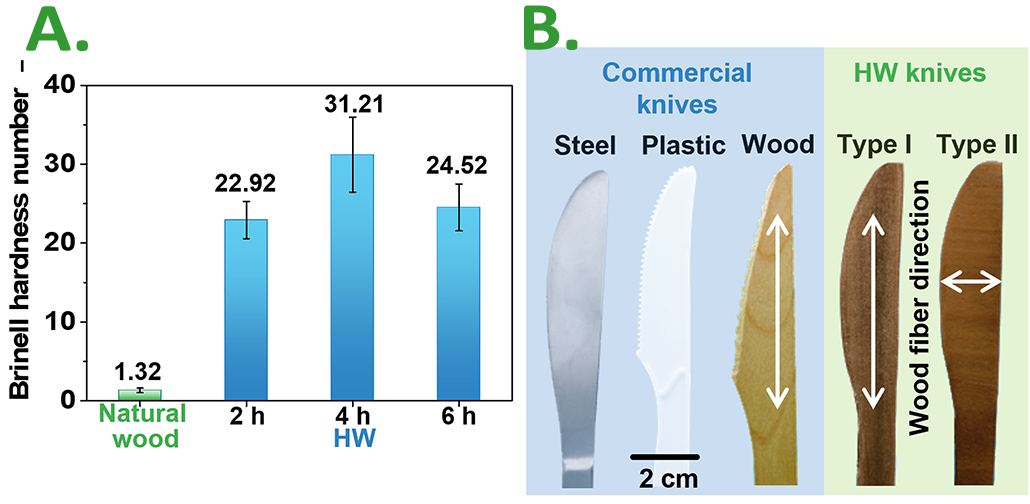
To measure sharpness, they pushed the knives’ blades against a plastic wire (Figure C). In some tests they pushed straight down (cutting without sliding) and in others they used a sawing motion (cutting with sliding). Sharper blades require less force to cut the wire.
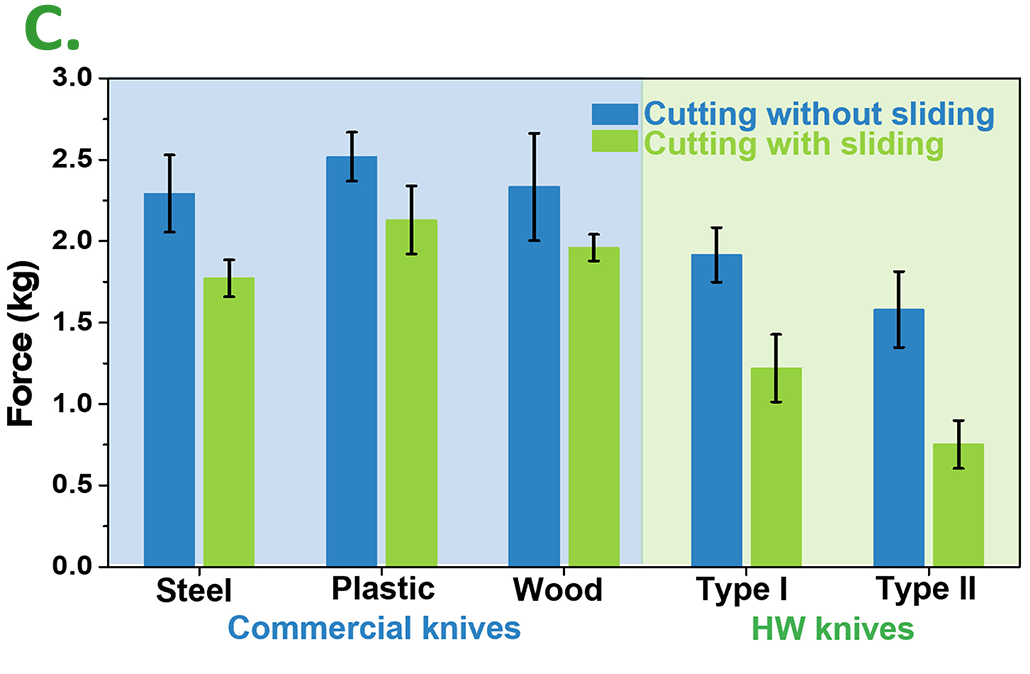
Data dive:
- Look at Figure A. What treatment time gives the hardest wood?
- How does the hardness change from 4 hours of treatment time to 6 hours?
- Divide the hardness of the hardest wood by the hardness of the natural wood. How much harder is the hardened wood?
- Look at Figure C, which shows the force required for each knife to cut a plastic wire. Sharper materials require less force (less pushing) to cut. What is the range of force values for commercial knives?
- Which knives are the least sharp? Which knives are the sharpest?
- Which motion, sliding or no sliding, requires more force to cut? Does this fit with your experience cutting vegetables or meat?