A better way to stop a bullet?
Teen’s data suggest the fabric in body armor would work better if it were woven differently
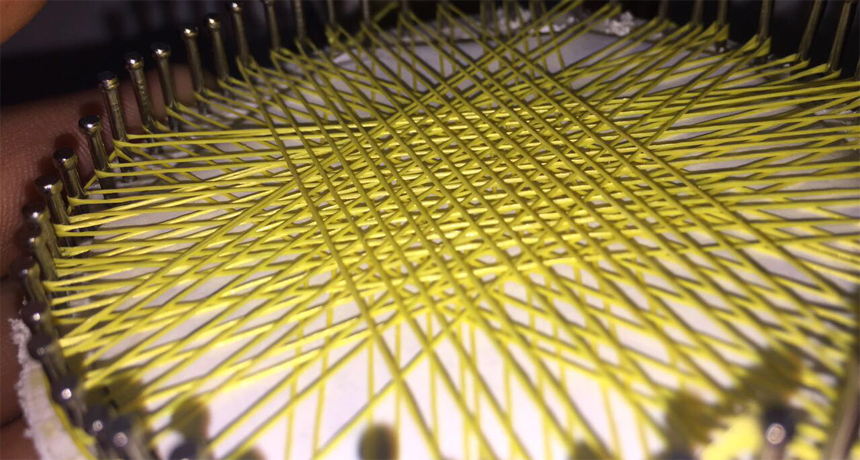
Body armor made with a three-directional weave (image) would provide better protection that that provided by the two-directional weave similar to what’s found in a window screen.
Lynn
By Sid Perkins
LOS ANGELES, Calif. — Body armor is a critical piece of safety equipment for police officers and military troops. It helps keep bullets and other projectiles from getting an opportunity to pierce flesh. But the fabric-based body armor could offer even better protection if it were woven differently, a teen’s new tests suggest.
The most common forms of body armor, including bulletproof vests, are woven from a super-strong plastic fiber sold under the trade name Kevlar. First developed in the 1960s, it is stronger than steel but weighs much less. The fibers in body-armor fabric typically run in two directions and cross at 90-degree angles, notes Lucas Lynn. He’s an 11th-grader at Wetumpka High School in Alabama. Such fabric typically has square holes in its mesh. It looks similar to the material used in a window screen, only it’s woven much more tightly. Lucas wanted to see if he could improve body armor’s performance by changing the fabric’s weave.
He purchased Kevlar fiber and used it to create two different weaves. One made the normal, two-fiber square mesh. The other used three threads that intersected at 60-degree angles. The mesh this created had triangular holes. Those holes also tended to be smaller and the weave tighter than in a two-fiber, 90-degree mesh.
Lucas covered each mesh with a mixture of powdered calcium carbonate (the same mineral as chalk) and a particularly viscous form of polyethylene glycol. It’s a common chemical used in both manufacturing and medicine. The resulting goopy mixture works as a shear-thickening liquid, the teen explains. That means it flows rather smoothly under slow and steady pressure, but stiffens greatly when something hits it suddenly — such a bullet.
Lucas tested his goop-covered meshes by shooting BBs at them. BBs are small, round projectiles that are often fired from a gas-powered gun or rifle. BBs typically range between 4.3 and 4.4 millimeters (about 0.17 inch) in diameter. But flying at about 190 meters per second (430 miles per hour), these tiny projectiles can pack a big punch, Lucas notes. So behind each mesh he added two layers of foam rubber. He placed a cardboard box behind that to catch any BBs that penetrated the foam.
The square-grid mesh didn’t stop any of the BBs from reaching the box, Lucas found. But the triangular mesh slowed down or stopped every BB. In only two cases did the BB shot make it to the second layer of foam.
Lucas showcased his research, here, at the Intel International Science and Engineering Fair. Created by Society for Science & the Public and sponsored by Intel, the competition lets students from around the world show off their winning science fair projects. (The Society also publishes Science News for Students.) This week, nearly 1,800 high school students from more than 75 countries competed for big prizes and the ability to display their research findings.
Lucas conducted additional tests by weaving fabrics out of 3.2-millimeter (0.125-inch) Kevlar cord. These fabrics, also coated with the goop, worked even better than those made of Kevlar thread. Again, the square-mesh fabric did not stop any of the BBs, while the triangular-meshed fabric stopped all six BBs fired at it. Two of the BBs even ricocheted, or bounced, off of the fabric. The teen concludes that his three-fiber weave provides better protection that one woven with two fibers.
UPDATE: For this project, Lucas received a $1,500 award at Intel ISEF from the Society for Experimental Mechanics.