Can concrete conquer air pollution?
In the lab, powdered concrete sops up sulfur dioxide
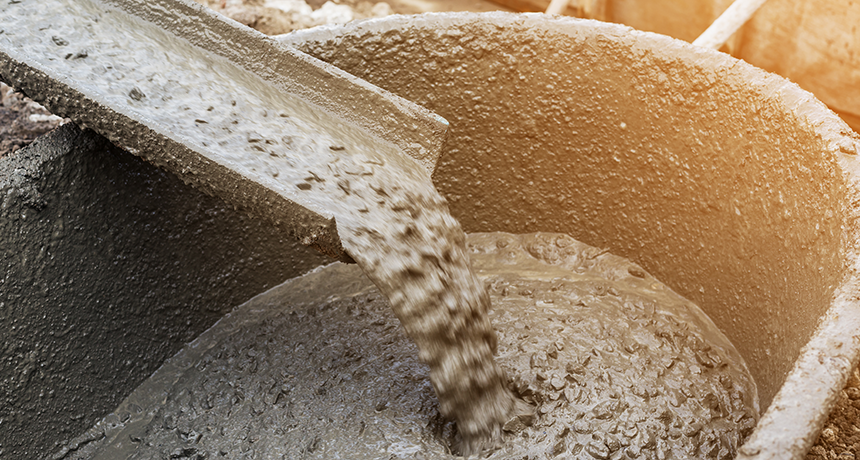
Concrete, once hardened and then powdered, may be able to remove certain pollutants spewed by electric power plants.
tortoon/iStockphoto
Share this:
- Share via email (Opens in new window) Email
- Click to share on Facebook (Opens in new window) Facebook
- Click to share on X (Opens in new window) X
- Click to share on Pinterest (Opens in new window) Pinterest
- Click to share on Reddit (Opens in new window) Reddit
- Share to Google Classroom (Opens in new window) Google Classroom
- Click to print (Opens in new window) Print
By Sid Perkins
From buildings and bridges to dams and driveways, people use billions of tons of concrete each year. Now this handy substance might find another use as well. Powdered concrete could collect harmful pollutants spewed by fossil-fueled power plants, a new study suggests.
Girish Ramakrishnan is a materials scientist at Stony Brook University in New York. Concrete can clean up some of these pollutants thanks to one of its ingredients — cement. That’s the stuff that slowly hardens and binds everything together.
In 2014, the Stony Brook researchers showed that powdered concrete can react with nitrogen oxides, often called NOx. These pollutants contribute to the formation of smog, a type of lung-choking pollution. NOx also can play a role in turning rainfall acidic. This can damage crops, buildings and more. But cement contains calcium compounds. And they will react with NOx, pulling them out of the air, Ramakrishnan and a colleague showed.
Curious, the team decided to see if concrete would do the same thing to another major air pollutant released by fossil fuel burning: sulfur dioxide.
Besides harming the environment, sulfur dioxide — or SO2 — can cause lung problems. In the air, sulfur dioxide helps create small particles of soot. As sulfur dioxide levels go up, so do cases of bronchitis, an inflammation of airways in the lungs. People with bronchitis often wheeze and cough.
To test the ability of concrete to pull SO2 from the air, Ramakrishnan’s team mixed up a batch of fresh concrete. Once it had hardened, they ground it into a fine powder. That increased the material’s surface area, explains Ramakrishnan. That extra surface area upped the number of sites where chemical reactions could take place between the concrete and air pollutants.
Each teeny gram of the team’s powdered concrete had a total surface area of between 8 and 10 square meters (86 and 108 square feet). That’s about the same as the floor area of a small room!
The scientists then packed about 3 grams (1 ounce) of this powder into a small tube to create a filter. This device was tiny — about the same size as a pencil eraser. Then the researchers pumped polluted air through it. Well, it was a gas meant to stand in for polluted air.
Normal air is mostly nitrogen mixed with oxygen. The researchers added SO2 but left that oxygen out (because otherwise it, too, might react with the pollutant they were studying).
The researchers then ran their mix of nitrogen and SO2 through the filter for about 8 hours. The concentration of SO2 was very low — only about 5 molecules of this for every million molecules of nitrogen. That may not sound like a lot, but it’s much higher than what is considered safe to breathe.
Afterward, the researchers looked at the filter under infrared light. If SO2 had reacted with the concrete, the interaction should have formed compounds called sulfates and sulfites. Those compounds absorb infrared light, Ramakrishnan explains. And the team’s instruments could monitor absorption to detect those compounds in the filter.
Those tests confirmed that SO2 indeed had been pulled out of the air and become bound to calcium-bearing compounds in the cement. Ramakrishnan and his team reported their results July 1 in Chemical Engineering Journal.
The team’s filter was very small, Ramakrishnan points out. This made it hard to precisely measure how much SO2 the powder-packed filter had removed from the gas. To get a better idea, the team is now testing larger filters. They hold 1 kilogram (2.2 pounds) of powdered concrete.
Outlook hazy
Not everyone has as rosy a view about the potential role of concrete in cleaning up pollution as Ramakrishnan does. Among these skeptics is Jeffery Roesler. He’s a civil engineer at the University of Illinois at Urbana-Champaign.
Most coal-burning power plants already remove a large fraction of the SO2 from their emissions. They do it using filters with relatively cheap calcium-containing substances, he notes. Those substances use the same type of chemical reactions as the concrete does. So it wouldn’t make sense, he argues, to make concrete just to grind it up into a more costly, less effective powder. No matter how well those concrete filters work in the lab, he says, they may cost too much to replace the older types already in use.
So why not recycle used concrete to cut the costs? Ramakrishnan says it might work, but not as effectively as new concrete.
Some nations, such as the United States, already set relatively strict limits on emissions of air pollutants. Concrete-based filters may not make sense in these countries, says Robert Farrauto. He’s an environmental engineer at Columbia University in New York City. Still, he adds, they might find use elsewhere. In other countries, where the levels of SO2 are higher, he says, using concrete might prove practical.
The team’s filters could offer another benefit as well. Powder particles in the used filters become covered with sulfates and sulfites. Those filters might themselves be recycled to make new concrete for roadways and other structures. Using them that way might reduce reactions with chlorine from chemicals like road salt, Ramakrishnan says. As he explains: If the calcium in the cement bound all of those sulfates and sulfites, then it won’t be available to react with chlorine. That, in turn, means road salt wouln’t damage roads or other concrete surfaces as much as it does today.
In the long run then, he argues, concrete-based filters might still save money.