Cool Jobs: Bringing you summer thrills
The designers behind fun rides and fireworks reveal some of their secrets
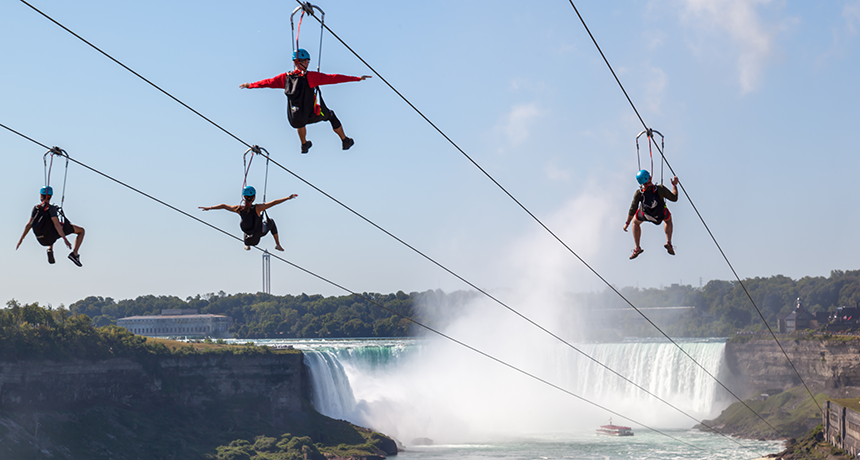
Sailing along a zip line can be a spectacular way to take in the local scenery.
JHVEPhoto/iStockphoto
By Gerri Miller
When Anya Lehrner was 12 years old, she fell in love with a Beast. This wasn’t the enchanted prince of Disney movies. The Beast is the world’s longest wooden roller coaster, located at Kings Island amusement park in Mason, Ohio. She was scared but worked up the courage to face down her fear. And she’s been riding coasters ever since.

“I stopped being afraid of roller coasters when I was a teenager. But they’re still fun to scream on,” says Lehrner. And now coasters are her job. As a design engineer for Skyline Attractions in Orlando, Fla., she builds roller coasters around the world — and, of course, rides them.
“I love the Incredible Hulk ride at Universal Studios in Florida. It’s not a slow climb. You blast up like a rocket,” she says. It may be scary, but it’s “more like controlled fear,” she says. “It reminds me of being a little kid and forgetting about everything,” she says. It’s all about laughing and having fun.
Roller coaster design, though, is more than just fun and games. To be a good designer, Lehrner has to draw on her knowledge of science, technology, engineering and math (STEM) to create rides that are both entertaining and safe. She’s not alone. STEM is also a key part of other park rides as well as those fabulous fireworks displays that can explode with color across the summer night sky.
Taking a ride
Lehrner had always wanted to design roller coasters. Even as a kid, though, she knew that there had to be more to it than just hopping on board. “I started thinking about how I would prepare,” she says. She looked to science and math. “I took advanced classes in algebra, geometry and trigonometry in middle school and high school. Then she took even more advanced math — calculus — and a high-level physics course.
She also visited theme parks as often as she could and researched the makers of those coasters online. When it came time for college, she went to the Colorado School of Mines in Golden. There, she got a bachelor’s degree in mechanical engineering.
Now Lehrner spends her days working with amusement parks to plan and build new coasters. These are coasters that are largely made of wood, except for a metal track on which the cars run. The basic design has been around for more than a century. Still, Lehrner notes, each one is different. “We use a lot of the same components and concepts. But they change with the terrain and layout. That tells us what the limits will be — how tight the curves and how high the hills are.”
Some parks want their coasters to be as scary as possible. That means big drops and quick turns and lots of inversions (when the ride goes upside down). Lehrner’s specialty is twisted wood coasters. “We wrap the track around itself and they’re lower to the ground, giving you the illusion you’re going faster than you really are,” she explains. “We shoot for a ride that’s fun for the whole family — fun and scary at the same time.”
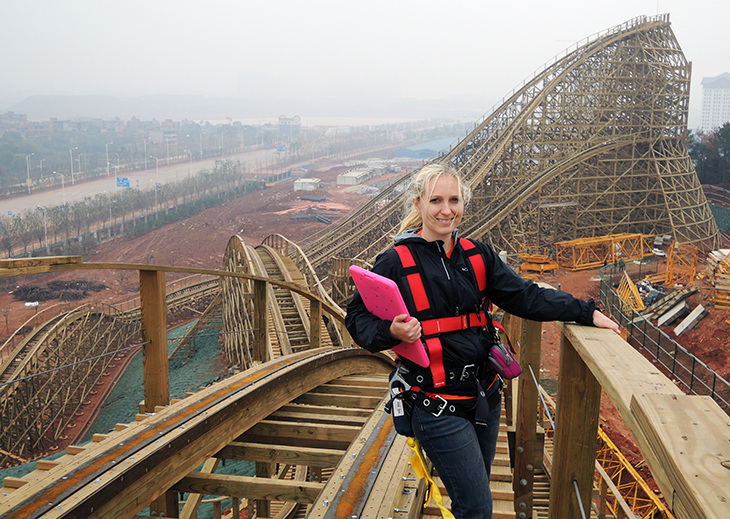
As you can imagine, “The most fun part of the job is when the ride is complete and we’re doing the final testing on site,” Lehrner says.That’s when her team gets to ride it. “But 75 percent of the time I’m at my computer, with deadlines and tasks to get done. There’s a lot of small stuff to keep track of. There are hundreds of parts that make up each ride and hundreds of drawings for each.”
For the InvadR coaster, at Busch Gardens in Williamsburg, Va., Lehrner and her team created something new. This coaster was a hybrid of wood and steel, another common building material for roller coasters. Designing it was a challenge because this was a new process. So, before construction started, Lehner’s team created a 3-D model of the ride. “It’s been a bit of a learning curve,” Lehrner says. That’s where computer graphics come in.
Before any construction gets underway, the team creates a 3-D model of what the ride will look like. This allows the engineers to make coasters even cooler, she says. How so? “You can use [this] technology to create more intricate, smoother-flowing rides.”
Safety, Lehrner says, “is our number one priority.” She must follow strict regulations, and all calculations and designs are carefully inspected. “If any one part of the system fails, there’s another to back it up,” she notes. Lap bars lock in place in several different ways, for example. And the structure is reinforced so that a couple of wooden boards can break and the ride will still be safe.
One big concern in coaster design is g-force. One g-force is the force exerted on an object by the Earth’s gravity at sea level. Two Gs, for instance, is twice Earth’s gravity. Too many Gs can be uncomfortable or even dangerous. To determine the g-force a rider will experience, Lehrner makes calculations based on speed, how tight the curves are and the shape of the track. “When we test the ride, we put sand bags or water dummies in the car for weight,” she says. “And we use accelerometers mounted on the cars to measure speed and forces.” An accelerometer measures changes in movement due to gravity or dynamic forces.
Lehrner says it’s never too early to look into careers that interest you. “Go to the library or use the internet to learn about companies and technologies. Take as much science and math as you can if you want to be in the engineering field,” she says. “If you’re really interested in something, go for it and pursue it. Jobs like this do exist!”
Lighting up the sky
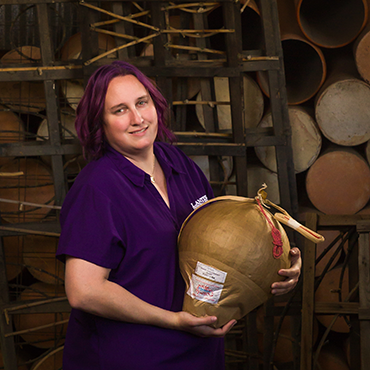
Business is literally booming for Catherine Lantis. She creates pyrotechnic displays that light up the sky with blasts of color as a designer for Lantis Fireworks and Lasers in Fairfield, Utah. She also runs the company, which her grandparents founded in 1945. And it’s every bit as much fun as it sounds, she says.
“I grew up watching what my dad did. It made me want to follow in his footsteps,” says Lantis. “I was finally allowed to shoot a show on my 18th birthday. And I’ve been doing it ever since.”
Lantis’ training was on the job, watching her dad and uncle. “But you do need to study to get your license.” Then, she notes, she had to “spend more time to qualify to run a show as the lead ‘pyro.’ The tests are different in every state.” Lantis has a college degree in business. But the chemistry classes she took in high school have helped in this career. “Chemistry is a big part of getting the colors, sounds and patterns,” she explains.
A basic firework is made of chemicals: potassium nitrate and charcoal or sulfur. By tweaking that recipe, Lantis can customize what someone on the ground sees. The chemical strontium carbonate produces the color red. Orange comes from calcium chloride and yellow from sodium nitrate. Barium chloride produces green and copper chloride blue. Purple is produced by a mixture of strontium and copper.
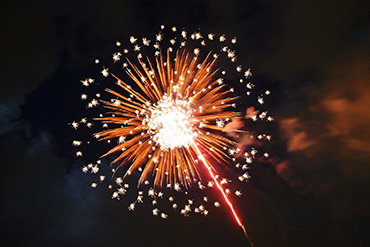
“To make the patterns, you use what we call ‘stars.’” These are metal salts that are packed into the fireworks. They range from the size of a pea to the size of a plum. “You place them in the design you want,” she says. For instance, “to make a heart shape, you’d set the stars in that pattern.”
Setting off a firework is a two-step process. The firing phase launches each rocket into the sky with a lift charge. That is made of gunpowder. Then a second fuse detonates. This one triggers the chemical reactions behind each distinct color, pattern and sound. At some shows, Lantis does this firing by hand. At others, a computer manages the launches. Either way, there’s a lot to consider.
“Some shows have more than one shooting site. Shows with music require special sequences to ensure the fireworks match up [to the musical notes].” Depending on how big the show is, she may need fewer than 100 explosive shells or many thousands. “No two shows are alike,” Lantis says.
One thing that doesn’t change is safety. “We work hard to keep everyone safe,” Lantis says. Crews train in safety procedures. Inspections are done at the site. Firefighters are kept on standby. Plus, she notes, “there are new products and safety features coming out all the time.”
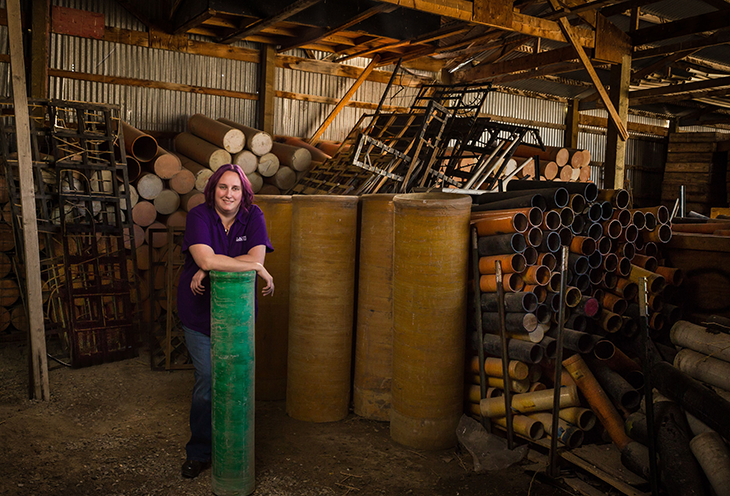
Lantis produces between 12 and 20 shows each year, mostly in the western United States. July 4 is the busiest, followed by Christmas and New Year’s. “But we are always busy getting our shows ready to go,” she says. Setting up a show takes all day long, usually in hot weather. “Then, after the show, you spend all night cleaning it up,” she says. “But seeing people’s happy faces and hearing their cheers makes this job all worth it,” she says. “I love what I do.”
Lantis has four children under the age of 9. They love going to her shows. “They tell me they can’t wait to be old enough to go shoot fireworks with me,” she says. “But they’ll have to wait until they are 18!”
Soaring through the air
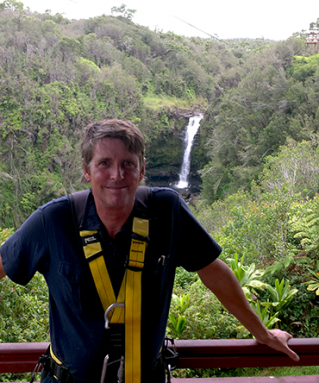
People can’t fly without external help, but racing through the trees on a zip line comes close. Fun and scary at the same time, a zip line sends a person down a cable high above the ground. And the popularity of zip lines has been soaring in recent years. There are now commercial zip-line attractions all over the United States and in many other parts of the world.
Zip-line consultant Michael Reddish has been building some of these attractions since 2002, when he built his first ones in Hawaii. “The scenery is really spectacular. You’re zipping over rivers or by the ocean,” he says. He has also designed zip lines for clients in Alaska, Canada and Mexico. He got his start when he rigged a rope between two trees at a YMCA camp in Arizona more than 40 years ago. “People hung on to both sides of a handkerchief to zip down it. It was 50 feet long.” That’s about 15 meters.
Today’s zip lines are longer and more sophisticated. They can reach 300 meters (1,000 feet) or more. A few are as long as 1.6 kilometers (1 mile). “It takes six to 12 weeks to build a zip line. I go to a site, look at a hill and see the zip line in my head,” Reddish says. “You can make a zip line work just about anywhere except for flat ground,” he says. Why? One side needs to be higher. You could build a tower and start the zip line there. But then you’d need a ladder, he notes. “And they’re hard for some people to climb.”
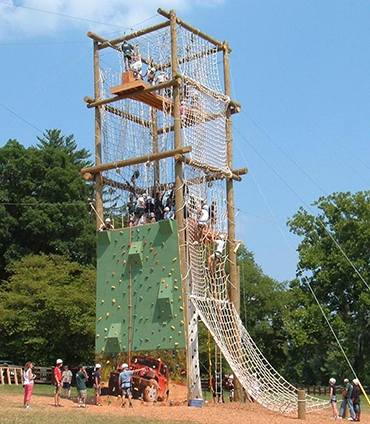
Once he sets the location, Reddish must calculate for a series of variables. And that’s where math and physics come in. The size and strength of the cable determine how much weight it can take. For example, a cable that is 1.2 centimeters (0.5 inch) with a strength of 4,500 kilograms (10,000 pounds) can take 900 kilograms (2,000 pounds) of weight, Reddish says. He also must figure for the amount of sag in the cable (think of a telephone line between poles) and the wind factor.
“At one zip line, we had a 20 mile-per-hour [32 kilometer-per-hour] headwind,” he notes. Here, the team “had to make the cable 10 percent steeper,” he says. If not, those winds would slow the ride down. (A headwind is a wind blowing directly into something.)
Weight of the riders is another important consideration. “You have to make sure your lightest rider will reach the end of it, even in a headwind,” Reddish explains. Most commercial zip lines require that riders be at least 20 to 30 kilograms (about 45 to 65 pounds). Rain also can affect riding conditions. Not surprisingly, people sail down a wet cable a lot faster than on a dry one, he observes.
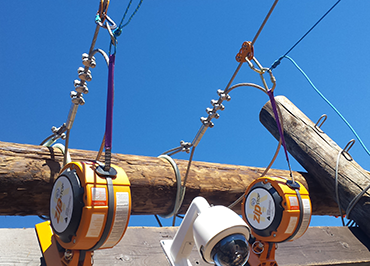
Everything must be tested over and over. You can’t risk riders hitting the end pole, he notes. So “you’ve got to have a foolproof double braking system.” To test a new system, Reddish sends sand-bag weights that are heavy enough to stand in for someone going down the line with a 16 kilometer-per-hour (10 mile-per-hour) wind at his or her back. “All the tests are recorded and documented,” he notes, and the equipment inspected each year.
These days, Reddish spends most of his time consulting, doing inspections of existing zip lines and building one or two new ones a year. Zip-line building is still a small field, and there aren’t any courses that will teach a person to do Reddish’s job. But he recommends studying applied engineering in college and learning about cable dynamics. Middle- and high-school math and physics are good preparation for that. “I was really into math in school,” Reddish says. “It’s so important in what I do.”
This is one in a series on careers in science, technology, engineering and mathematics made possible with generous support from Arconic Foundation.