Father and son harness magnetic fields for new type of 3-D printing
Working in their basement, they designed a system to build complex objects, layer by layer, out of metal
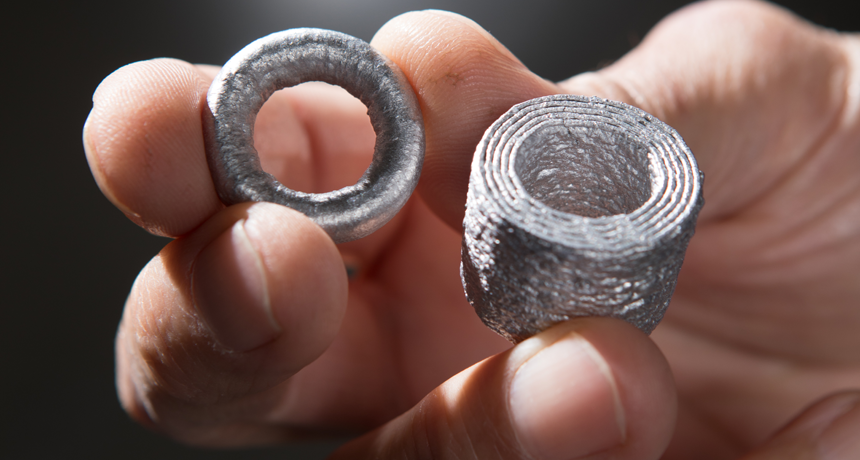
Scott and Zack Vader printed these aluminum cylinders in their basement using their novel 3-D printing process. They also can create more complex, custom designs.
Douglas Levere
Working in their basement, a father and his son in Buffalo, N.Y., have created a new way to make metal items: They build them, one layer at a time, out of tiny bits of molten metal. Doing this relied on some creative use of physics.
The duo designed a machine that employs magnetic fields to squeeze liquid metal into drops of precise sizes. Squirted onto a surface, those drops harden to build a solid metal object.
Their method is a type of “additive manufacturing,” or 3-D printing. A 3-D printed object starts with a computer file describing its eventual size, shape and other details. A computer program digitally “slices” a model of the design into thin layers. Then it tells a printer where to place drops of material. One by one, these drops combine to form each slice of the object. The process repeats to add more slices on top. By this means, the object builds up, layer by layer.
3-D printing is good for making one-of-a-kind items, complex designs or design samples. Those items can cost a lot to make. Standard factories are rarely set up to make novel or one-off items; they instead make huge numbers of similar things. “Ink” for 3-D printing can be liquid plastic, foods or even cells. Printing with metal has been possible too, but so far it also has proven tricky.
One common way to print metal objects layers a fine metal powder onto a base. Then a computer directs lasers to melt a pattern into the powder. It then cools into a hard base layer. The steps repeat to build new layers atop the older ones. But the metal powder needs special safety precautions. The waste powder must be handled carefully. And the lasers are costly.
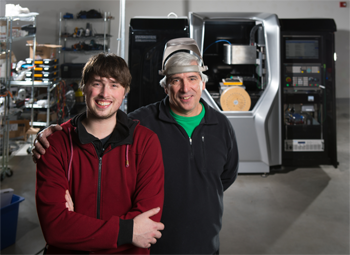
Scott Vader is a mechanical engineer. Several years ago, while his son Zack was studying to become a mechanical engineer, they decided to invent a new type of small electric generator. They researched how to make its parts out of aluminum. And that’s when they learned about the laser-melt printing and its drawbacks.
Zack remembered seeing a show on television. It showed the military working with electromagnetic coil guns. Electricity flowing through coils in the gun creates a magnetic field. That field shot out aluminum ammunition.
“I thought that if they’re controlling aluminum using coils, why don’t we use that,” recalls Zack. Inspired by that concept, he and his dad switched their plans from building a generator to making a new type of 3-D printer.
Squeezing metal with magnetism
Their printer has a thumb-sized nozzle with a ceramic chamber. That ceramic can withstand high temperatures. An electric coil wraps around the chamber. When an electric current flows through the coil, it produces a magnetic field.
(That part of the design is similar to what happens if you coil copper wire around a nail and run electric current through the wire. The electric current makes a magnetic field. Small iron objects will stick to the nail. Take away the nail, and the magnetic field is still there.)
The Vaders’ printer fills the nozzle chamber with melted aluminum wire. Then, an electric current runs through the coil. The magnetic field from the coil induces, or creates, an electric current within the aluminum inside the nozzle. The current in the aluminum flows in a circular motion. It is opposite to the current going through the coil. And that current in the aluminum produces its own magnetic field. The two magnetic fields interact. That creates pressure within the melted aluminum. And that pressure squeezes drops of molten metal out of the nozzle’s tip.
To make a specific object, the printer must push out droplets of just the right size and at just the right time. The Vaders’ machine does this with pulses of electric current. Those current pulses produce a pulsed magnetic field and pressure. Timing the pulses just right controls how and when the metal “prints.”
“The pressure pulse lasts less than a millisecond,” says Edward Furlani. He’s a physicist at the University at Buffalo who helped with the project. “You’re producing droplets on demand.”
Quality control
The printer spits out about 1,000 metal drops per second. “We can make a one-inch tall, one-inch diameter test cylinder in about three minutes,” says Scott Vader. (That’s about 2.5 centimeters by 2.5 centimeters.) But because it is so fast, any problem can quickly clog the printer nozzle.
Chi Zhou is an industrial engineer at the University at Buffalo. He helped with the software to control the printer. He also found a quick way to check if the droplets are coming out just right.
A light emitting diode, or LED, sits to one side below the printer’s nozzle. A receiver sits on the other side. A computer constantly checks how much light reaches the receiver. As a droplet falls, it blocks some of that light. “According to the energy change, we know the behavior of the droplet,” Zhou says. If a droplet isn’t right, it will block too much or too little of that energy. And if that happens, the computer signals that something is wrong and shuts off the printer.
Story continues below video
Prospects for the system
Parans Paranthaman is a materials scientist at Oak Ridge National Laboratory in Tennessee. He has worked on other additive manufacturing projects and gave his personal view on the Vaders’ design. For 3-D printing with aluminum, “this method they have developed is really good,” he says. But, he adds, the current set-up won’t work in all instances.
Metals with higher melting points would require more energy to reach those higher temperatures, Paranthaman notes. Some alloys (mixtures of metal) would likely cause problems, he says. And the method wouldn’t easily allow 3-D printing of certain magnets, he notes, which can be destroyed by high heat. One of Paranthaman’s 3-D printing projects did create magnets. But to do that, he avoided very high heat. His group used pellets made of powdered metals and nylon, which melted into a liquid that could be squirted through a nozzle.
Scott Vader says that his team is now testing a new printhead that can work at hotter temperatures, up to 1,200° Celsius (about 2,200° Fahrenheit). His group also wants to try working with other metals, such as bronze, copper and silver.
For now, Scott says the process will “make 3-D metal printing much more accessible.” Researchers have shown interest in it. So have people who make consumer goods, car parts, medical devices, tools and other products.
The Vaders presented their design at the TechConnect World Innovation Conference and Expo in Washington, D.C., last May. The process and the latest updates will be discussed during a program at this year’s TechConnect conference in Washington on May 15.
“Everybody thinks that everything’s been invented before. But, no,” Scott Vader says. “Two guys in their basement can still come up with something pretty significant that is in big demand.”
This is one in a series presenting news on technology and innovation, made possible with generous support from the Lemelson Foundation.