How to recycle ‘nonrecyclable’ plastics
A new process could allow reuse of certain plastics that would otherwise be trashed
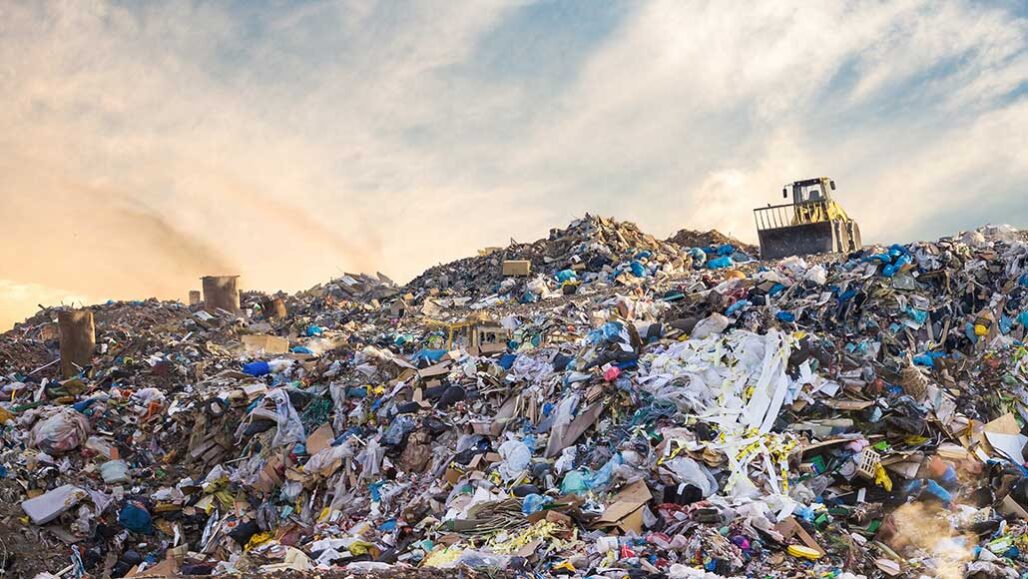
New research could provide a way to keep certain types of nonrecyclable plastics from ending up in landfills.
vchal/iStock/Getty Images Plus.
A new process could cut down on the amount of plastics buried in landfills. The idea: Convert some types that can’t be recycled into a type that can be heated and then reformed.
Of the more than 35.4 million tons of plastic produced each year in the United States, the share that gets recycled “is relatively small,” the Environmental Protection Agency finds — just 8.4 percent as of 2017. More than one-third, it adds, eventually ends up sent to landfills as waste.
Plastics can take hundreds of years to degrade, or break down chemically. And when buried in landfills, they take up valuable space. Other plastic wastes end up in the oceans, streams and other waterways. There they break apart into tiny particles, called microplastics. Some contain harmful additives. Microplastics also can provide a surface for other pollutants and microbes to cling to. And those plastic bits can build up in some animals, too.
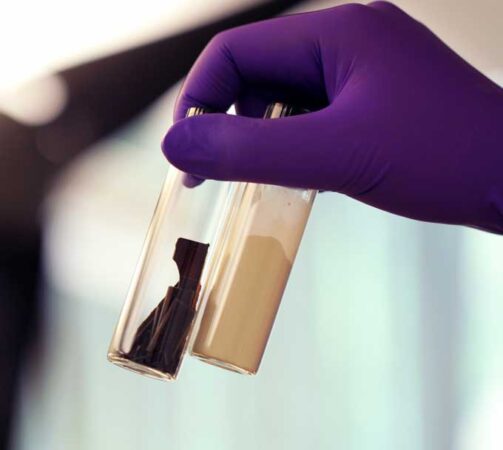
A few types of plastics can be melted and reformed into new items. Many drink bottles, LEGO blocks and other products (labeled with a 1 or 2) can be recycled in this way. Their molecules are basically long chains of repeating groups of atoms.
So far, though, there’s no way to recycle what’s known as thermoset plastics. The prefix thermo- refers to heat or temperature. The process to make these plastics takes soft solids or liquids and then cures them, usually by heating.
That curing forms crosslinks among groups of atoms in this plastic. That network of linked atoms makes these lightweight plastics strong enough to withstand impacts. They’re also good insulators for heat and electricity.
“Most of the plastic components in an aircraft are thermoset materials,” says Ica Manas-Zloczower. She’s a chemical engineer at Case Western Reserve University in Cleveland, Ohio. “You have thermosets in cars. You have thermosets in buildings.” Widely used, these plastics show up in products ranging from cell phones to wind-turbine blades.
Their permanent crosslinks have meant these plastics can’t just be melted and reshaped. But that may soon change.
Are vitrimers the solution?
About 10 years ago, researchers in France developed plastics with releasable crosslinks. They’re known as vitrimers [VIH-trih-murs]. Think of a folk dance where people change partners, says Manas-Zloczower. Here, groups of atoms say goodbye to their partners as their crosslinks break apart. Then the groups pair up to crosslink with new partners.
Last year, Manas-Zloczower and Liang Yue, also at Case Western, were part of a team that developed a process to convert thermoset plastics into such vitrimers. Now, this group has improved the process even more. Plastics made this way can be recycled again and again.
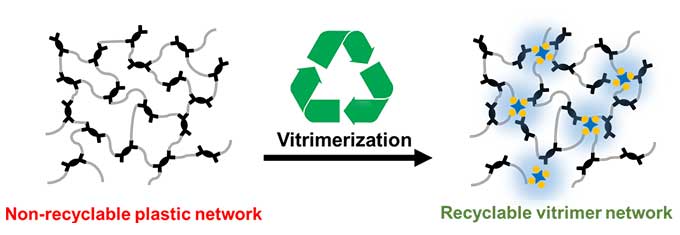
The team combined bits of one type of thermoset plastic with a tiny amount of a zinc-based compound. They added the mix to a ball mill. That’s a high-energy grinder with uses balls made of metal or some other durable materials. The ball mill’s mechanical energy turns the plastic into a fine powder. The process also creates radicals — molecules with one or more unpaired outer electrons.
“Radicals are very reactive,” Yue says. In the mix, the radicals react with other molecules to convert crosslinked chemical bonds into the non-permanent types found in vitrimers. This powder can now be pressed into a heated mold to form a new shape. Later, the new plastic can be heated and molded again, without adding more of the zinc material.
In that way, he notes, these plastics “can be reprocessed over and over.”
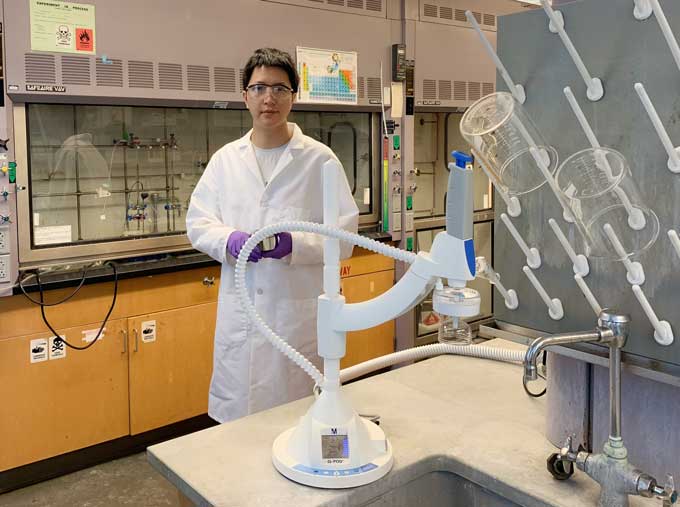
A similar approach can work for other types of thermoset plastics, too, Manas-Zloczower says. Those might rely on chemicals other than the zinc compound. Some vitrimer plastics might even perform better than the original thermosets for some uses. Others might perform less well. For instance, one might withstand greater force before it breaks — but be less flexible.
The team is now looking for business partners to help the group scale up its new process. More research on possible effects from different additives in these plastics also will be needed, Yue notes. His group described their new recyclable vitrimer plastics in the June 16 ACS Macro Letters.
“The idea to convert existing thermosets into vitrimers is very appealing,” says Tanja Junkers. She’s a polymer chemist at Monash University in Clayton, Australia. Even though it is a new process, it could be applied to polymer wastes produced a long time before, she explains. But first, a full assessment of this technique and the new plastics will need to be fully tested, she says.
The team’s approach is “relatively simple” compared to some methods, Junkers adds. “But it is exactly that simplicity that allows it potentially to be applied in the real world.”