Light-sensitive ‘ink’ gives 4-D printing more wiggle room
By mixing technologies, this 4-D printer can create objects that move in new ways
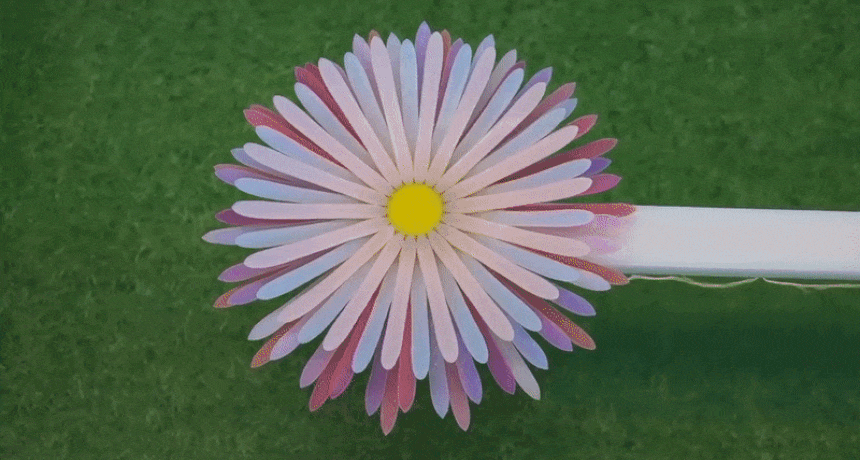
Using new technologies, researchers have 3-D printed a flower whose petals curl when immersed in water. This shows how 3-D printing can be used to print 4-D objects.
H.J. Qi et al.
By Ilima Loomis
Unlike their rigid 3-D cousins, 4-D-printed objects can flex. Some can totally reconfigure their shapes. People usually design these to respond to some sort of facet of the environment. They might open or transform when exposed to heat, for instance, or when dropped in water. Until now, however, there were only a few ways they could move.
Scientists at the Georgia Institute of Technology in Atlanta have now developed a novel “ink.” When combined with a new method of printing, it opens up hundreds of new options for movement.
The Georgia Tech team showed it off March 21 at the spring national meeting of the American Chemical Society in New Orleans, La.
Epoxy is a strong and versatile material used in many applications. H. Jerry Qi and his team had been developing an epoxy resin to use in printing. But to harden, Qi notes, the resin has to be exposed to heat for many hours. That’s just too long when each 3-D printed layer must fully harden before the next can be laid down.
Qi, a materials scientist, invented a way around that hurdle. His innovation: Mix the resin with another material that could be cured — turned into a solid — using light. Now each layer can be set with light, then fully hardened later with heat. This two-stage process really sped up the printing rate.
While testing different ways to cure resins with light, Qi’s group also found that the light‘s intensity (how bright it was) could affect how hard a resin became. They could vary the lighting to make some parts of a printed object harder and more rigid, while others stayed soft and flexible. That prompted them to apply this to the printing process. Their goal was to create an object where parts of it might be hard, while other parts were soft enough to serve as movable joints.
And it worked.
Qi showed that he could print objects that would bend and flex in a range of different ways. Some joints were stiffer, others looser.
Still, it needed tweaking. The hardest part of the printed object could be only some 20 times harder than the softest part. While good, that was not good enough for Qi’s group. It wanted to be able to have access to a broader range of stiffness and flexibility while designing an object.
The researchers’ inspiration — or “aha” moment — came when they tried combining their two innovations. By varying the light intensities as their new epoxy resin printed, they were able to get a much greater range of softness. Now, the stiffest part of a printed object can be 600 times harder than its softest part.
The Georgia Tech team developed the process together with scientists at the Singapore University of Technology.
Printing objects with several materials
Many 3-D printers today can make objects from plastic. Or metal. Or living cells. Even from cheese. But Qi introduced a new 3-D printer at the same meeting that could build objects from a range of different materials at the same time.
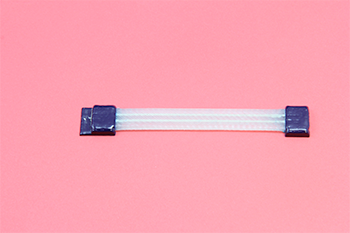
One example was a plastic ribbon that has electrical wires running through it. “Each layer you print can have multiple materials,” he explains. This, he says, makes it “a powerful manufacturing tool.”
Consider objects used in electronics. They contain multiple materials that sit side by side, such as the metal wire surrounded by insulating rubber that might be embedded into a plastic structure. Most 3-D printers can now print those different materials only as separate layers. But Qi’s new printer can lay them down, side by side, all within the same layer. Objects that today must be assembled piece by piece in a factory, might one day be printed out as needed, layer after layer.
That’s an important step for 3-D printing, says Geoffrey Spinks. He’s a materials engineer in Australia at the University of Wollongong. Right now, the range of materials that can be printed together is limited, he says. “If you want to have plastic and metal printed together,” he says, “you can’t do that.” But he says that what they have already shown, “in my opinion, is a step toward that goal.”
Qi hopes one day to combine technologies again. He’d like to use the variable-light hardener in a multi-material printer. It would give his new device another unique trait — the ability to print multi-material objects with a wider range of motion.
This is one in a series presenting news on technology and innovation, made possible with generous support from the Lemelson Foundation.