Nanowires made from silver are super stretchy
Atoms on their surfaces flow like a liquid to heal flaws and allow wires to triple in length
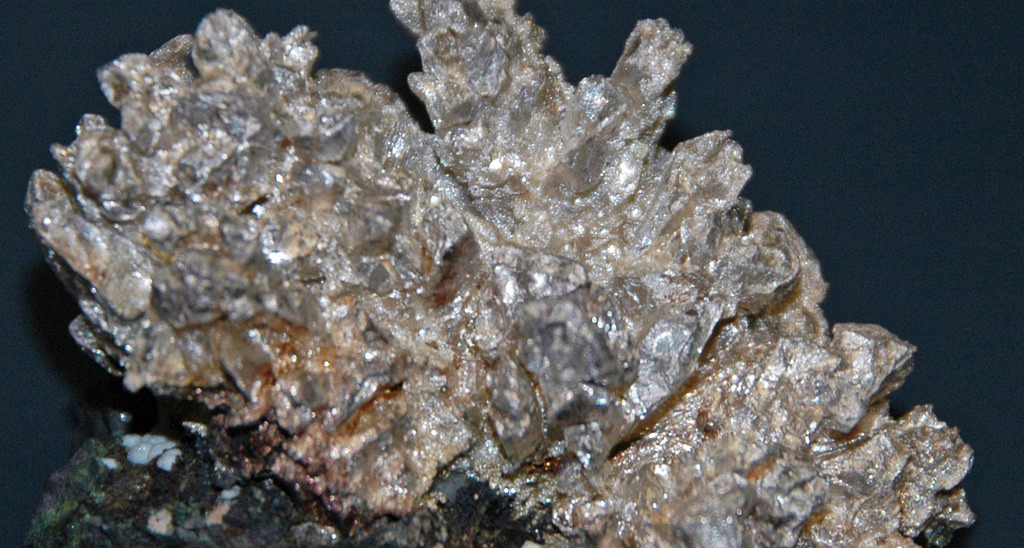
This naturally occurring chunk of silver came from Michigan. Scientists used much, much smaller pieces of silver to make surprisingly stretchy nanowires.
James St. John/Flickr (CC BY 2.0)
Share this:
- Share via email (Opens in new window) Email
- Click to share on Facebook (Opens in new window) Facebook
- Click to share on X (Opens in new window) X
- Click to share on Pinterest (Opens in new window) Pinterest
- Click to share on Reddit (Opens in new window) Reddit
- Share to Google Classroom (Opens in new window) Google Classroom
- Click to print (Opens in new window) Print
By Sid Perkins
Many metals can be fashioned into wires. You just have to stretch out a piece of the metal until it’s long and thin. Keep pulling, and the wire will eventually break. But new research reveals that when wires are extremely small, they can be super-stretchy. That’s especially true when they’re made of a single crystal of silver and stretched slowly. These wires can stretch to almost three times their original length before they snap, new data show.
And that’s a big deal for engineers. They could use that sort of stretchiness to design flexible electronics that resist damage.
Many researchers have studied the strength of wires made of soft metals, says Frederic Sansoz. He’s a materials scientist at the University of Vermont in Burlington. Soft metals such as gold, silver and platinum are called ductile. That means they can stretch a long way — from a fat chunk into a long, thin wire — before breaking.
On average, the smaller a wire is, the stronger it is compared to its diameter. Why? In general, smaller wires have fewer flaws that can make them snap. That pattern continues down to a diameter of about 40 nanometers. (That’s very small! Even the thinnest human hair is more than 400 times thicker.)
The inspiration
Other studies had shown that silver wires smaller than 40 nanometers in diameter act much differently, Sansoz notes. If their diameter is less than 10 nanometers, they can deform and then slowly return to their original shape. “Even though it’s a solid, it kind of behaves like a fluid,” he explains.
Since silver wires act so differently at small and large sizes, Sansoz and his teammates wondered what happens in the middle. They wanted to study how silver wires behave when their diameter is between 10 and 40 nanometers. That hadn’t been studied before.
The researchers made very tiny silver wires. They fashioned each from a single crystal of silver. That meant the wires would be flawless on the inside, he says. They might have rough surfaces, but they’d be the strongest wires possible.
In some tests, the researchers pulled on the wires slowly. In others, they stretched the wires more quickly. And the speed of that stretching had a big effect on how quickly the silver wires snapped.
When they stretched the wires so they got more than 2 percent longer each second, the wires broke quickly. At those speeds, they now realize, any flaw on a wire’s surface became a point of weakness. The wire narrowed at the flawed spot until it looked like a wasp’s waist. Then it snapped.
When stretched more slowly, a wire lasted longer.
The team then used a computer to simulate what was going on. It has now pointed to the answer. As the wires stretch slowly, atoms on their surface can flow like a liquid into any weak spots. This helps “heal” flaws in the wire. So, there are few places where the wire can thin enough to fail. In some cases, the silver nanowires nearly tripled their original length before breaking.


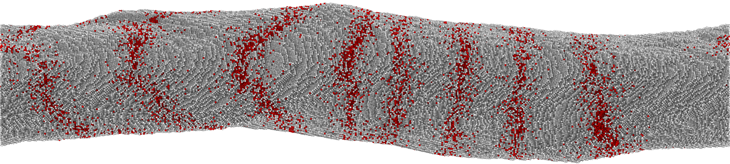
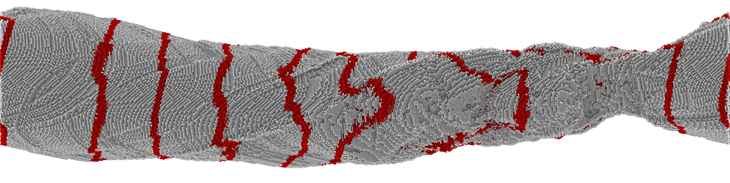
L. Zhong et al., Nature Materials (2016)
Sansoz’ group reported its results in the April Nature Materials.
This could lead to new products
The results are important because a lot of engineers are now trying to design stretchy or flexible electronics, says Yong Zhu. He’s a materials scientist at North Carolina State University in Raleigh. “This work shows that under the right conditions, it’s possible to achieve larger-than-expected elongations,” he notes. “That’s remarkable!”
Now that researchers know super-stretchiness is possible, Zhu says, engineers can take advantage of that when they design circuits. The stretchier that small wires are, he says, the more flexible or resistant to damage a device can become.
This is one in a series presenting news on technology and innovation, made possible with generous support from the Lemelson Foundation.