New coating for metals could cut engine wear
Substance creates a slick and tough film that decreases friction, extends life of oil
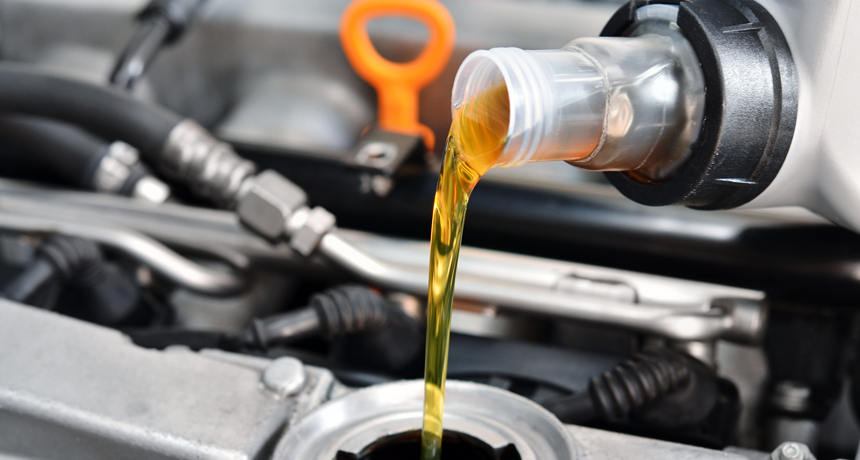
Researchers have developed a new coating for engine parts that may reduce how often drivers must change their oil.
Siarhei Hivoin/iStockphoto
By Sid Perkins
Car engines need oil to reduce friction between moving parts. This lubrication keeps the parts cool and cuts down on engine wear. Now, researchers have developed a new hard coating that would be applied to engine parts before they leave the factory. This is no ordinary coating. It’s an “active” surface that’s permanently bonded to the auto parts. And it doesn’t just sit there. It interacts with motor oil to create a slick carbon film that cuts friction better than the oil would alone.
The new coating may decrease how often a driver must change the oil, scientists say. It also could help reduce the need for metal-based additives in motor oil. Today, those additives make used oil difficult to recycle.
In the extreme heat and pressure inside a running engine, those metal additives are useful. They bond to auto parts and create a slick and protective surface. That layer — together with the slippery oil — reduces friction and wear inside a vehicle’s engine, explains Ali Erdemir. He’s a materials scientist at Argonne National Laboratory in Illinois.
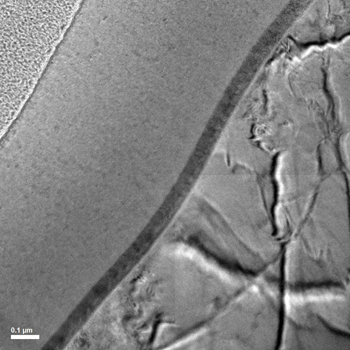
The metal additives’ lack of eco-friendliness, among other factors, helped inspire Erdemir and his team to develop their innovation. The researchers created a metal-nitride coating that contains an ingredient that interacts with motor oil — and removes the need for the additives.
The reactions the coating triggers create a surface film on moving parts. That film is less permanent than the layer that forms using today’s oil additives. But the new film is also self-renewing, Erdemir notes. So when it eventually wears away, a metal ingredient in the coating — a catalyst — breaks down more oil to rebuild the carbon film.
In other words, “The film is self-healing,” says Robert J.K. Wood. “It’s brilliant. This is an exciting idea,” says the mechanical engineer from the University of Southampton in England. The Argonne team’s new coating creates a film that is both low-wear and low-friction, he notes: “That’s a combination that we don’t have now.”
Erdemir’s team described the details of its new coating in the August 4 Nature.
How it works
Oil is made of hydrocarbons — long chains of carbon atoms to which hydrogen atoms are bound. Each carbon has two hydrogen atoms attached to it except for the last carbon on each end of the chain. Those end-carbon atoms are each bonded to three hydrogens. A metal ingredient in the team’s new coating helps strip away the oil’s hydrogen atoms. It then breaks apart the remaining carbon chains to make smaller carbon chains out of them. Those bite-size carbon chains create the lubricating film between the engine’s moving parts.
About four-fifths of the carbon in the film includes the same sort of chemical bonds found in graphite. (That’s the form of carbon used to make pencil lead. Graphite is also commonly used as a non-liquid lubricant for moving parts.) The remaining fifth of the film’s carbon atoms have the same sort of chemical bonds found in diamond. (Diamond, another form of carbon, is one of the hardest natural substances on Earth.)
The Argonne group has designed and tested two versions of its coating. In one recipe, the oil-chopping element is copper. In the other, it’s nickel. Both metals work the same way, Erdemir notes. They act as catalysts to accelerate the chemical reaction that breaks down the oil. However, as catalysts, they also do not get consumed by the reaction itself. That means the catalyst survives and continues to help break down oil whenever it is needed.
One big question, says Wood, is whether the coating will last a long time when exposed to the high pressures and temperatures inside an engine. Sometimes catalysts lose their punch over time, he points out. Also, he wonders, what happens if the coating completely wears away?
But after testing, Erdemir’s group is convinced its coating should indeed last a long time — maybe a decade or more for normal drivers. The coating is between two and three times harder than steel, they estimate. Plus, because it experiences little or no wear, a coating just a few micrometers thick (thinner than the diameter of the finest human hair) should last long enough for a car to drive a few hundred thousand kilometers.
This is one in a series presenting news on technology and innovation, made possible with generous support from the Lemelson Foundation.