Bioplastics could put some shrimp in your Barbie
Teens turn to natural materials to make ‘greener’ plastics
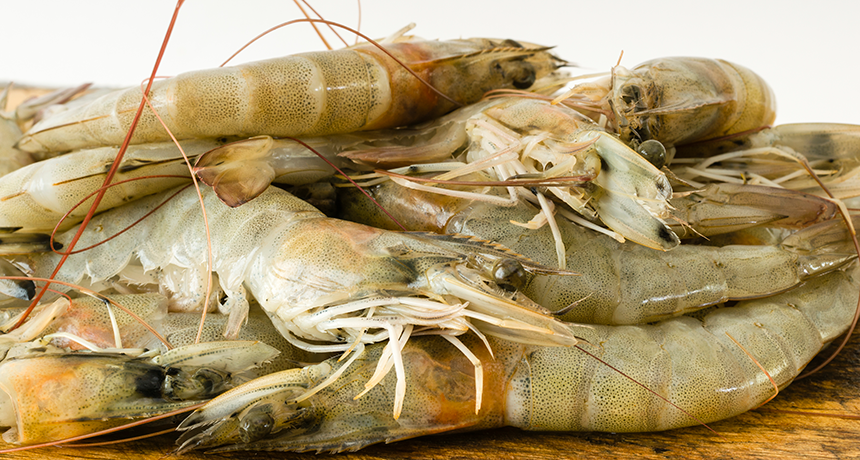
A material in the shells of shrimp is a key component of a new, ecofriendly bioplastic created by an Australian teen.
VINODKPILLAI/ISTOCKPHOTO
By Sid Perkins
PITTSBURGH, Pa. — Chemists have been working on ways to “green” our environment by creating materials that will break down, not persist as long-lived trash. Two teens have now unveiled their own innovative contributions. They made plastics from ingredients that are themselves wastes (not the fossil-fuel-based hydrocarbons used for most plastics).
Plastics have long been considered wonder materials. They weigh little, are relatively cost and have a broad range of potential uses. Many also last almost forever. That last trait is both a blessing and a curse.
In many places, plastics litter the environment. Many roadways and city streets are strewn with bags and other types of plastic debris. Large zones of the open seas are aswirl with tiny bits of plastic. Landfills are growing fat with discarded plastics. Bits of plastic even show up in the deepest, most remote spots in the ocean — and in the guts of fish.
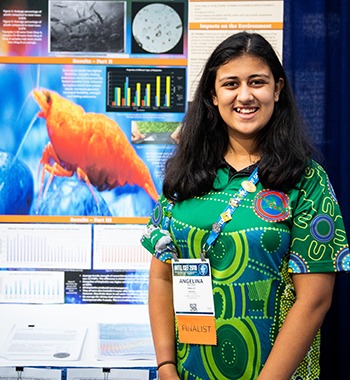
To help limit this waste buildup, researchers have been exploring ways to make plastics biodegrade. These strategies rely on microbes in the environment to help digest wastes — break them down — into simpler materials. One key to succeeding, researchers suggest, might be to make the plastics from something other than petroleum products.
Angelina Arora, 15, is an 11th grader at Sydney Girls High School in Sydney, Australia. Mohammad Arafa and Jassin Zaki, both 18, are 12th graders at 6 of October STEM Egypt School in Giza, Egypt. All three rose to the challenge of designing green plastics that will naturally break down in the environment.
The three also described their new bioplastics here, three weeks ago, at the Intel International Science and Engineering Fair (ISEF). They were among almost 1,800 finalists from 81 nations, regions and territories. The winners collectively took home about $5 million is prizes and scholarships.
About one in every three finalists took home some sort of award. Angelina was part of that group. For her project, she earned a fourth-place award in environmental engineering. It came from the Intel Foundation and was valued at $500. Angelina also snagged a scholarship from Arizona State University.
Society for Science & the Public created ISEF in 1950 and has been running the event since then. (The Society also runs Science News for Students and this blog.) Intel sponsored this year’s competition.
Plastics from the sea
Shrimp are tasty, which is why people eat millions of tons of them each year. What people can’t eat, however, are the animals’ tough shells. They are chock full of a material called chitin (KY-tin). It develops when chemical reactions inside certain cells take molecules of glucose, a simple sugar, and attach other molecules to them — then string the resulting units into a long molecule. It’s known as a polymer. The flexible but resilient polymer forms the shrimp’s external support system (similar to those on insects). It’s known as an exoskeleton.
Usually, shrimp shells go to waste, Angelina notes. But she’s come up with a way to use them in a plastic. First, she grinds the shells into a powder. Then she soaks the powder in acid. This removes some of the minerals that were in the shells. Now she soaks what’s left in an alkaline bath to remove other minerals. The only thing left after that step is pretty much pure chitin, she says.
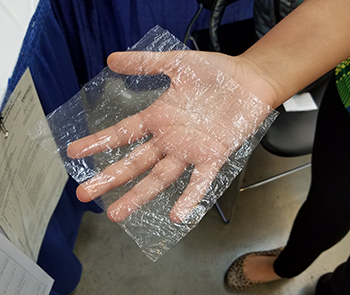
Angelina’s plastic also contains a substance called fibroin. It’s a protein in the silk created by spiders. It’s also a big fraction of the silk in the cocoons spun by the larvae of certain insects. For her project, the teen got her fibroin from low-quality silkworm cocoons. Typically, only the best cocoons are used for the silk used to make fabric, she says. The rest, like shrimp shells, often are trashed as a waste.
For her plastic, Angelina simply blended the chitin and fibroin. Then, she pressed the mix into thin sheets and let them dry.
The results were impressive. Sheets of her bioplastic were more than 90 percent as strong as low-density polyethylene (LDPE). That’s the plastic used to make many grocery-store shopping bags, among other things. Slightly increasing the thickness of her polymer should yield bags just as strong as those used now, she says.
But unlike those made from LDPE, bags made from Angelina’s plastic should not generate large amounts of long-lived trash. In fact, her tests show that her bioplastic dissolves in sea water more than a million times faster than LDPE does. So, any bags that ended up in the ocean shouldn’t stick around forever to be eaten by marine creatures. Instead, they’d dissolve in about five weeks.
Plastics from a tree
Most plastics are made from chemicals derived from petroleum. Few microbes eat such plastics, notes Mohammad. So, these plastics don’t tend to break down in the environment. What’s more, he notes, there is very little recycling of plastics in Egypt, where he lives. To keep plastics from taking up precious space in landfills, he and Jassin, a classmate, came up with the idea for a biodegradable material made from plants.
The teens started with banana peels. They’re full of starch, a natural polymer, Mohammad notes. They added in a slick, sweet liquid called glycerol (GLIH-sur-awl). It’s a plasticizer, a chemical that makes materials soft and pliable. Their goal was to make a plastic that would last at least two months. So the students also mixed in a preservative to keep the plastic from decomposing too quickly. (This chemical is called sodium metabisulfite.)
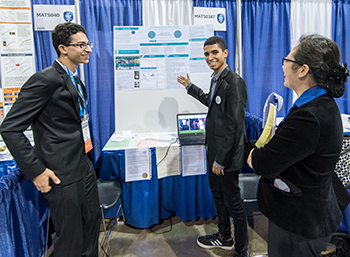
Mohammad and Jassin tested several recipes. Then they compared their strength and flexibility to that of containers made with a type of plastic commonly used for bottled water or milk. Their best results came when their plastic included less than 8 percent glycerol.
Unfortunately, their best-performing plastic was still only three-quarters as strong as the plastic used by businesses today. For a container to be just as strong as those used now, it might need to be up to twice as thick. Adding a little clay might also strengthen their plastic, Mohammad and Jassin say.
Overall, the teens believe their new bioplastic shows promise. When buried in soil, the bottles they made broke down in less than 5 months. But sitting on a shelf, the bottles were able to hold their shape and strength for at least two months before they started to break down. And even if there’s a bit of clay in the recipe, it wouldn’t harm the environment when the plastic eventually decomposes.
Overall, bioplastics offer hope for greening the environment, these young scientists report.
Follow Eureka! Lab on Twitter